Elements of Delcam’s PowerShape, PowerMill, and PowerInspect are brought together with a new file format designed for electrode design.
Delcam has launched a new integrated solution for the design, machining, and inspection of electrodes. Delcam Electrode is a combination of elements from Delcam’s PowerShape CAD software, PowerMill CAM system, and PowerInspect inspection software.
The production of electrodes is a key stage in the manufacture of many types of tooling; Delcam believes this new product will increase efficiency and reduce lead times across a number of industries.
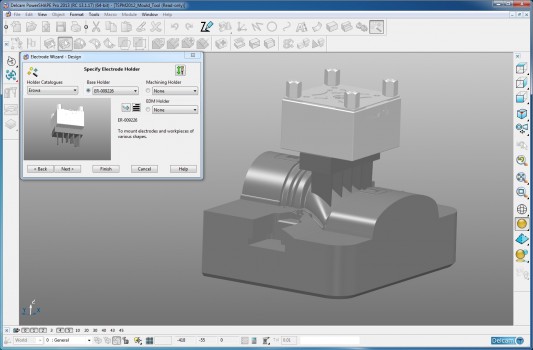
At the heart of Delcam Electrode is a new file format, the .Trode file. The file definition specifies all the information for an electrode project, including the electrode design, the machining and inspection information, plus the set-up sheets for its manufacture and use.
The initial design stage of the process benefits from the direct modeling tools available within PowerShape. Users can define the region where the electrode will be used, extract the shape needed to produce the required feature in the part, and then edit the design to provide clearance from the main surface of the tool and to blend it into the blank size needed to fix the electrode into its holder.
Analysis tools are available to check that the draft angles and minimum radii used in the design will not cause downstream problems, while the ability to simulate the action of the electrode ensures that it will operate as expected. To speed the design process further, catalogs of blanks and holders are included from Erowa, Hirschman and System 3R. Users can add their own standard sizes to these databases.
Once the design has been finalised, the necessary spark gaps can be specified to provide the machining offsets required in PowerMill to cut the roughing and finishing electrodes. Inspection points can also be added so that the measurement of the electrode in PowerInspect can be automated. Then, set-up sheets for the electrode’s manufacture and use can be produced automatically, either to a standard format or to a user-defined template.
Companies that produce multiple electrodes of similar sizes from the same material can develop templates within PowerMill to machine them in a standardised way. Burn, clearance and blank faces of the electrode are automatically color-coded within PowerShape so that they can be recognised within PowerMill. The size of the material block and the spark gaps for the electrode family are also read from the .Trode file and applied to the toolpaths automatically. Once the templates have been created, generating the machining toolpaths becomes a fully-automated process.