Utah’s Lifetime Products became Delcam’s 40,000th customer when it selected PowerMill as its new CAM software.
Lifetime Products is a Utah-based manufacturer of outdoor products ranging from swing sets and basketball hoops to lawn furniture and storage sheds. Almost all of the design and manufacturing in done in the United States, using contemporary CAM products and methods.
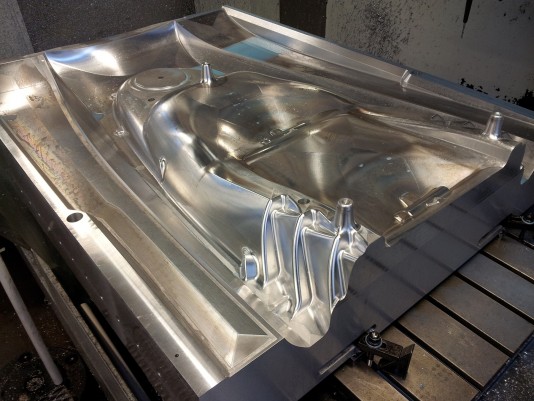
The Lifetime Products machine shop, staffed by 21 experienced machinists is an integral part of the company’s success. The machine shop purchased its first Mazak computer numeric controlled (CNC) milling machine more than 20 years ago, which was just recently sold to make room for a new and bigger Mazak. Today, the company owns four Mazak vertical machining centers, including two Nexus VNC-510Cs, a Nexus VCS-410A, a VTC-300C and a Mazak QuickTurn Nexus 300 turning center. Lifetime also has four HAAS VF-9 machines for milling its moulds. The company is expanding this department further, installing a new HAAS VS-3 in early October to meet the growing demand for moulds.
Just recently, Lifetime Products expanded its offerings to include kayaks in its line of outdoor products. The company uses PTC Creo for design but wanted a state-of-the-art CAM product to go alongside it. Since the company’s designs can be quite complex, the machine shop had to find something that would take the large files without difficulty, something that could compliment its current processes but extend its CAM capabilities. After reviewing a number of CADCAM products, Lifetime decided on Delcam. The timing was right for Delcam, as Lifetime Products became their 40,000th customer.
“What attracted us to Delcam first was the PowerMILL CAM package, especially the speed with which it can calculate toolpaths,” says Dennis Norman, mold design engineer at Lifetime Products. “It is not uncommon for software companies to say they have fast toolpath calculation but PowerMill backs this up with multi-threading and background processing. It automatically performs complex calculations in the background while we can continue to work on other toolpaths.”
Norman says PowerMill’s user interface allowed Lifetime to take on machining of the kayak mould quite quickly. “Once the project was done, we were very impressed,” said Charles Monsen, lead programmer. “We had never had a mold come off the machine that looked that good. It was quite a project to take on for our first time but working with PowerMill made it easy. The toolpaths looked impressive and the finished product was very smooth.”
Lifetime Products has since purchased Delcam’s FeatureCAM, the feature-based CAM system, for its shop floor operators. Kelly Martinez, machine shop manager, says, “We were impressed with the diversity the company could offer us and how attentive the people there are to our needs.” Most of the job-shop parts machined by Lifetime Products had been programmed using the Mazatrol off-line programming system for Mazak CNC machines.
Operators at Lifetime Products are now doing all of their own programming with FeatureCAM. “Before we added FeatureCAM, our shop floor operators could only program with Mazatrol. Now that they have picked up FeatureCAM so quickly, they can easily take a program and put it on another machine if necessary or program a part themselves, even parts with complex surfacing,” says Martinez. “Previously the shop floor operators would have to get one of the programmers, who are very busy programming complex molds, to do work on smaller surfacing projects. Now we can do a lot more programming right on the shop floor.”