Belshina of Belarus was able to bring all mold design, reverse engineering, and CAM prep in-house with Delcam software.
Belshina is one of the largest producers of automotive tires in Europe, both in the number and the size of the tires it manufactures. The company makes more than 200 different types of tires in three plants: one for mass production of car tires; one for buses, trolley-buses, lorries and tractors; and one for the largest tires for vehicles for earth-moving and quarrying. A fourth plant manufactures and repairs molds for the other three sites.
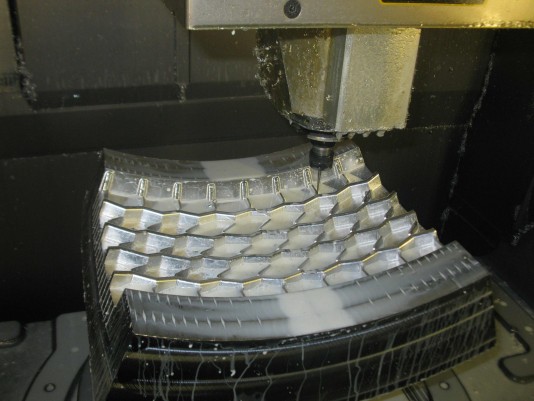
The company first invested in Delcam software in the 1990s, buying Delcam’s original DUCT system to give it the ability to program the first five-axis machine tools used in the moldmaking plant. At that time, the plant only produced around sixty molds each year, with the remainder of the company’s needs met by subcontract manufacturers.
At the turn of the century, Belshina made the transition from DUCT to Delcam’s PowerSHAPE CAD software and PowerMILL CAM system. The company steadily added more seats of both programs as it increased its manufacturing capabilities and the number of molds being produced. It has now reached sufficient capacity to be able to manufacture all its molds in-house and no longer uses subcontractors.
During the same period, the company investigated ways to improve its quality and consistency. In 2006, Belshina added a Cimcore inspection arm, together with PowerINSPECT for inspection and PowerSHAPE Pro for reverse engineering.
The most recent addition to the mouldmaking plant was a special four-axis machine tool from Taiwan, purchased in 2011 to mill inscriptions and trademarks onto the surfaces of molds. Belsina added an extra seat of PowerSHAPE and PowerMILL, plus PowerINSPECT On-Machine Verification, for this machine.
At the start of 2012, Belshina undertook an evaluation of its complete set of CADCAM software as part of a continuous development review. Following this review, the company ordered four seats of the FeatureCAM feature-based machining software and its first seat of ArtCAM for artistic applications, such as engraving of logos and trademarks.
When asked about his company’s long relationship with Delcam, Valery Saprykin, the Manager of the technology bureau at the plant, commented, “As soon as we started working with the Delcam staff, we realised that the company had very professional software developers. We have received exceptional support in solving the problems within our manufacturing plant. Whenever we have a problem, we can always find a solution from Delcam and Adequate Systems, the company’s representatives in Belarus.”
“Until now, we haven’t found any complex technical problems that we couldn’t solve with their help,” he continued. “We appreciate greatly such cooperation and partnerships.”
Currently, the factory produces more than 300 molds each year, with the growing demands of the parent company constantly requiring an increase in the number of molds to be manufactured.
“The reliability of the software, plus the variety of machining strategies, allows us to optimise the productivity of our equipment and meet the increase demand for molds each year, and to ensure that our quality levels are maintained,” said Mr. Saprykin.