Everybody wanted to talk about Catia V6 at this year’s Catia Operator’s Exchange (COE) Conference. Some manufacturers are creating new products in V6, others remain cautious.
By L. Stephen Wolfe, P.E.
The annual spring conference of the Catia Operator’s Exchange (COE) provides an affordable opportunity for customers of Dassault Systèmes’ flagship Catia CAD software in the Western Hemisphere to learn about recent advances and planned improvements and share experiences about the most recent releases. Catia version 6 was the talk of this year’s event, held April 23-26, 2012 in Las Vegas.
V6 is a radical departure from other 3D CAD systems. Instead of storing geometry in files managed by a computer’s operating system, Catia V6 stores geometry, part attributes, and assembly relationships in a database managed by Dassault Systèmes’ Enovia V6 product data management software (a direct descendent of MatrixOne, a PDM system dating from the early 1990s).
According to Dassault Systèmes’ executive vice president, Etienne Droit, the principal advantages of V6 over Catia V5 and all other CAD systems are:
- Improved performance, especially when designing complex products with geographically distributed teams.
- Improved reliability. Mean time between failure (MTBF) is between 120 and 150 hours, compared with 80 to 100 hours for Catia V5. Droit expects MTBF to reach 200 hours by the end of 2012.
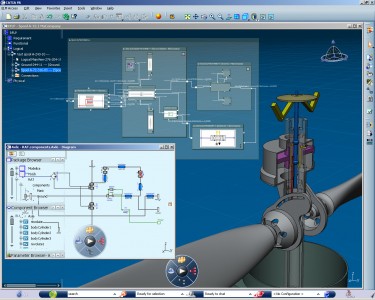
Improved performance ought to interest typical Catia customers whose companies design and manufacture complex products such as aircraft, automobiles, industrial machines, military vehicles, ships, and trains. However, until recently, these customers have resisted entreaties to move to V6. Speaking at the 2009 COE conference in Seattle, Kevin Fowler, vice president of systems integration and process tools for Boeing’s Commercial Airplane division, said his company needed to recoup its investment in migrating from Catia V4 to V5 before considering a move to V6. Today Boeing people say their company still has no plans to move to V6.
Other Dassault Systèmes customers have taken the more radical step of announcing plans to migrate to Siemens NX instead of dealing with the complex transformation of their data-management systems required by V6. Such customers include Daimler Corporation, Chrysler Corporation, and Huntington-Ingalls’ Newport News Shipbuilding division. H-I’s Ingalls division in Pascagoula, Mississippi announced plans to move from V5 to a combination of AutoCAD and ShipConstructor, an AutoCAD application.
At this year’s COE, customers seemed more agreeable to considering V6 than they were in prior years. V6 hands-on classes and lectures were well attended, and customers seemed eager to learn about the new software.
Representatives of two US customers, Textron’s Bell Helicopter and Cessna subsidiaries, presented their experiences migrating to V6 from systems that employ a combination of V4 and V5 models. Bell’s Jim Maestas said his company is using V6 to design its first all-new commercial helicopter in 20 years, the Bell 525 Relentless.
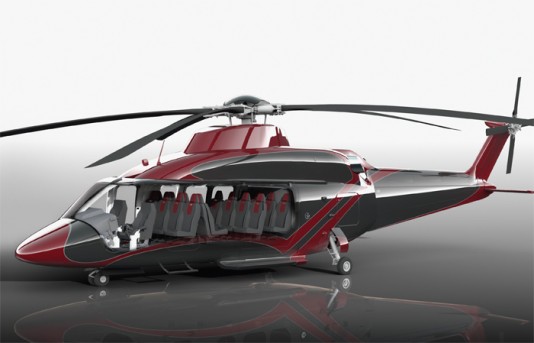
Bell is currently employing Catia V6 release 2011, which has been superseded by releases 2012 and 2012x. He characterizes the 2011 release as immature, even though V6 was announced in 2008. Bell had intended to use Catia V5 and Enovia LCA for a new helicopter design a few years ago, but when the program was cancelled, so was the V5 rollout. As a result, most of Bell’s historical CAD data is in Catia V4 or Siemens NX version 5.
Maestas says previous Catia V5 users find V6 easy to learn. It employs part-construction methods nearly identical to V5. The biggest procedural changes are in the ways assemblies are put together. Instead of employing the geometric constraints found in most other CAD systems (coincident, concentric, offset, etc.), V6 employs what Dassault Systèmes calls “engineering connections.” These relationships resemble the kinematics joints found in V5.
The absence of files is another aspect that requires user training. Instead of saving a file, designers “propagate” changes to their designs. Because each part is a database object, it must have a unique name. Parts employed in assemblies can’t be deleted from the database. Designers must “own” parts they create and can lock them to prevent changes by others. Only owners or database administrators can unlock parts. Instances of assemblies locked by somebody else cannot be updated even though the designer has access to the part being changed.
Copying parts also causes trouble if designers don’t understand the intricacies of the V6 database. Maestas says people have unwittingly duplicated entire sections of the aircraft and replaced them. “Do not duplicate from the explorer window,” he intoned. “Otherwise you can [inadvertently] duplicate the entire aircraft.”
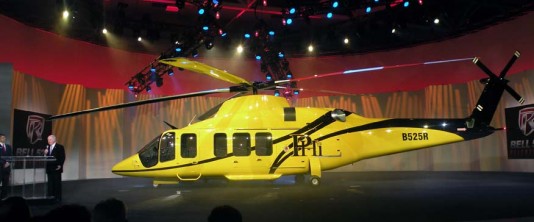
Maestas says Bell designers complain about the number of clicks to accomplish anything in Enovia V6. Nevertheless, he says it is more usable than Enovia LCA, the PDM software Bell uses with V5.
Outstanding capabilities of V6 include searching by date, version, or release status. Designers also can search for parent assemblies in which each part or subassembly is used. It’s possible to search for parts in 3D space by specifying a zone, box, sphere, or offset volume around a part and see the context of the entire product. Designers also can subscribe to parts or assemblies and be notified when they are changed.
V6 performs well, according to Maestas. Designers in India are finding no significant latency when opening drawings or models stored near Ft. Worth, Texas. In contrast, V5 customers report increasing lag times as designers get farther from the main database server.
Maestas also pointed out shortcomings of the new product. Tubing and harness tools are missing from the 2011 release. The Composite Workbench is “not robust,” he said. Measure tools don’t work as well as they did in V5. And despite its power, the advanced search window sometimes behaves strangely.
Cessna Latitude
Craig Hull of Cessna Aircraft gave a presentation about how his company is using Catia V6 to design a new executive jet, the Citation Latitude. Like the Bell 535, the Latitude was supposed to be an all-new design. But shortly after the project started, executives decided to re-use the wing and empennage designs of an older model, the Citation Sovereign.
Because the Sovereign was designed in Catia V4 with updates in V5 and because the Sovereign is still in production with part changes occurring regularly, Cessna needs to keep its existing Catia V4 VPM system in production as the Latitude is being designed. It was not feasible to migrate all of Cessna’s historical data to V6 in time to support the Latitude’s development schedule. Consequently, Cessna has to share CAD models among the V4, V5, and V6 versions of Catia.
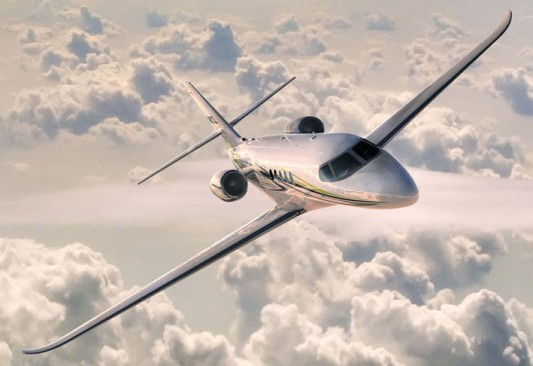
Called coexistence, the method of sharing data among three Catia versions turned out to be more complex than expected. Hull devoted most of his talk to the subtleties of doing so. Hull takes exception to Etienne Droit’s claim that importing V5 data into V6 is “a piece of cake.” “I’d accept that if he’d said fruitcake,” Hull quipped. “There are hard, chewy bits in the middle.”
Coexistence actually involves migrating all V4 and V5 data to Enovia V6 with all the attendant errors listed below. The difference is that coexisting data is treated as a copy whose master is a V4 or V5 model in an older PDM system. So if a coexisting model needs to be changed, the change must be made in the legacy Catia system. However, V6 lacks implicit controls to prevent users from changing coexisting data. Consequently, system managers must make sure that V6 users don’t have permission to change V5 models. Setting up these permissions for a bulk data transfer requires writing business-process scripts and debugging them.
Simple feature-based V5 parts may slip easily into V6, although the process involves “ripping each file apart,” in Hull’s words, to store its components as V6 objects. But parts with embedded Visual Basic scripts can have syntax errors. Sheet-metal parts may lose their design-table column headers. Electrical parts may suffer unspecified errors, and parts in some assemblies may be missing.
Moving V4 files to V6 also can be troublesome, Hull said. Assembly constraints may not translate perfectly, and V4 mockup data also causes problems.
Hull recommends that customers who are planning to set up systems that allow V4, V5, and V6 data to coexist should take the following actions:
- Find a person knowledgeable about how your Catia data is organized to be a coexistence administrator.
- People setting up the coexisting systems need to coordinate the people responsible for V6 implementation and training.
- V6 users must be properly trained about how to use V5 or V4 data in their designs. For example, they should be taught not to modify V5 product structures in V6.
- Set up all V5 data to co-exist, and only then transfer ownership to the V6 users as they need it.
- Decide which attributes in your VPM system you need in the V6 system. Don’t try to bring them all because, once imported into V6, they can’t be removed.
- Budget liberally for test environments, including hardware and software.
- Coexistence is a temporary solution. Try to migrate all users to V6 as soon as possible.
Asked if Catia V6 enabled Cessna to design its new plane faster, Hull replied, “I’ll tell you in three years. We haven’t gone wildly off schedule yet. But it is my experience that you don’t get the full benefit of new tools on the first job. The bigger benefits will come on future airplanes.”
Other technical challenges
Neither Bell nor Cessna has yet grappled with how to share data with suppliers who use file-based CAD software from Dassault Systèmes or other vendors. Dassault announced recently that Catia V6 R2012x will be able to exchange data bi-directionally with an upcoming release of V5 dubbed V5-6R2012x.
But one knowledgeable customer who has looked at the process says the “engineering connections” that fill the role of assembly constraints in Catia V5 and other systems don’t translate. Consequently, although V6 assemblies can be written as V5 CATproduct files with all the parts in proper orientation, there are no constraints holding them together.
Managing CAD models in a relational database has a different set of complexities from historical CAD and PLM. For instance, in typical CAD and PDM systems, designers can check out models, make copies, and change them to try new ideas. Throughout this process, the designers save their models to their desktops or file folders on their hard drives. If they come up with a design they like better, they can rename it and check it into their PDM systems.
With Catia V6, there are no files and no places to store designs while one tries them out. To “propagate” a part, it must have a unique name and be part of a project. According to Laurent Gascon of PCO Innovation, French automaker Renault persuaded Dassault to create the concept of a “work space” in Catia V6 R2012x that would enable designers to try new concepts without cluttering up the main product structure of their car models. The workspaces also provide useful ways to share with suppliers only those portions of a vehicle relevant to the parts they might supply.
Setting up workspaces requires system managers to write business-logic scripts that define workspaces and people who can access them. The scripts aren’t hard to write (at least for someone as computer-savvy as Gascon), but learning to use these procedures takes time and costs money.
Commercial considerations
Aside from the technical challenges posed by a V5 to V6 migration, customers have also been miffed by Dassault Systèmes’ commercial terms for the new software. Catia V5, like most other CAD software, is licensed on a simultaneous-user basis. This scheme allows designers who don’t use Catia around the clock to share licenses with others in their organizations. But because V6 is a database application, users must have unique log-in names to use it. So Dassault Systèmes licenses it on a named-user basis, a method more common to PDM licenses.
Dassault’s initial named-user pricing would have increased the cost of V6 for most customers. Recently, however, Catia pricing policies have become more accommodating.
Named-user licensing also complicates system administration. Bell Helicopter has two people assigning named-user licenses. Licenses are assigned for 30 days and can’t be released before that period is up.
Making it work?
Despite the challenges suffered by early V6 adopters, it appears that most Catia customers will eventually move to V6. Enovia V6 is receiving generally more favorable reviews than Dassault Systèmes’ older PDM systems such as SmarTeam, LCA, and VPM.
Allowing Enovia to manage parts without the added complexity of assembly files ought to simplify both the programming by Dassault Systèmes and the administration by customers of V6 systems. Storing part attributes in a database instead of part files should simplify searches and allow future Dassault Systèmes applications easier access to that data for other purposes. If V6 can enable multiple designers in remote locations to work on large product assemblies without performance degradation, it should justify itself to makers of complex products on the basis of schedule and labor savings.
Folks at large automobile and aircraft manufacturers have suffered through successful transitions from the early days of CADAM mainframe drafting software through upgrades to Catia V3, V4, and V5. There seems little doubt that these bright people (who make up the bulk of the COE membership) will make V6 work as well or better than previous releases if they continue to have faith in Dassault Systèmes.
Catia sales have grown modestly in recent years. Much of the increase was generated by Dassault Systèmes collecting the gross margin that once accrued to IBM. In the past 12 months, Catia sales rose just over 7.5% measured in Euros. It’s not clear how much V6 will increase Catia revenue above the recent trend line even if existing V5 customers convert to it.
The principal benefits of V6 accrue to makers of complex products. Most of these outfits already have some sort of CAD and PDM system, and few are inclined to switch brands. If Dassault Systèmes can demonstrate that V6 is much more efficient than Siemens NX or PTC’s Creo, it might entice some of these customers to join the Catia family. But the evidence of this superiority is still neither clear nor persuasive.
Among startups and smaller companies that supply industrial giants, V6 is likely to appear overly complex from the perspectives of both designers and computer-support people. Dassault Systèmes plans to address the support issue by offering V6 as an online service. But at this writing, such a service has not been offered, nor is it clear that it would be compelling if it were available. Even without the complexities introduced by its file-free methods, Catia V6 is not easy to learn and use. The interface is a welter of peculiar icons and work benches arrayed around a mysterious compass whose purpose is unclear.
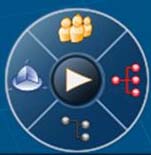
Fortunately Dassault Systèmes and its family of sophisticated manufacturers have both the time and the money to get V6 right. Etienne Droit told the COE audience that Dassault Systèmes is committed to supporting Catia V5 until at least 2020. Moreover, in contrast to statements by the previous Catia president, Jacques Leveillé-Nizerolle, Dassault Systèmes executives at this year’s conference said the Catia team will continue to add V6 design features to V5 in order to maintain bidirectional compatibility between the two releases.
For the next few years, the favored configuration among Catia customers is likely to be Catia V5 coupled with Enovia V6. By evolving toward this configuration, Catia customers will be better positioned to transition to V6 when the business case becomes clearer.
L. Stephen Wolfe P.E. is the 2004 award winner of the CAD Society Lifetime Achievement Award, a consulting engineer registered in the state of California, and one of the world’s best-known reviewers of engineering software. Wolfe holds a master’s degree in Mechanical Engineering from MIT, and a BSME from Northwestern University. He also attended the University of Chicago graduate school of business. He is a consulting analyst for Jon Peddie Research.