Toolpath improvements and optimization of calculations are also included in the new release.
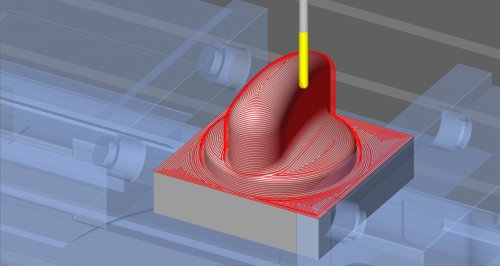
An update to Esprit computer-aided milling software includes a new 3-axis global finishing cycle, a solution for steep/shallow milling of complex part geometries. Other new features include toolpath optimization and better handling of wire profiles in electronics.
DP says global finishing optimizes machining by applying the most appropriate toolpath to complex parts based on an analysis of the model and a single threshold angle. Z-level cutting passes are applied to steep areas and boundary offset passes to shallow areas using a logic engine that gives priority to continuity of toolpath between steep and shallow areas for smoother finishing. A timesaving option constructs toolpath to machine over openings and holes in the CAD model without stopping or retracting the tool.
The 2017 version of Esprit also includes optimization to the primary calculation routines for turning CAD geometry into milling instructions. Up-to-the-minute intelligence about the shape of in-process stock is now built into facing, pocketing, and contour milling for faster, more reliable programming. The stock automation engine inside Esprit 2017 underwent a refactoring to drastically reduce calculation times from minutes to seconds for facing, pocketing and contouring operations. The same refactoring was applied to Esprit’s 3-axis roughing to compute in-process stock in dramatically less time, even on complex parts.
Awkward profiles in wire EDM parts are now cut more efficiently with new support for open profiles in EDM pocketing. When a profile is interspersed with small or oddly shaped openings, the wire can be programmed in Esprit 2017 to ignore those openings for a simple slug drop, then followed up with precise no-core pocketing that burns away only the small pockets of material that remain.