Using software designed for toolmakers instead of programmers made the difference.
The toolmakers at G. Parker Aero Tooling Solutions were getting frustrated with the rising backlog of projects not being completed in a timely fashion. The problem was a bottleneck in programming the ten computer-aided machining (CAM) units. The two seats of their existing software was complicated to use, leading to downtime for some milling units waiting for new instruction codes.
The company, which has been based in Accrington in the Northwest of England for over forty years and is now in its second generation of family ownership, produces a wide range of tooling, including jigs and fixtures, exclusively for the aerospace industry. It has been closely involved in designing and manufacturing tooling for many of the world’s most prestigious aircraft programs, including all Airbus platforms, plus the Eclipse and Honda VLJ programs. Virtually all of the tooling is made as a ‘one-off’ so developing the most efficient machining approach for each project involves a steep learning curve.
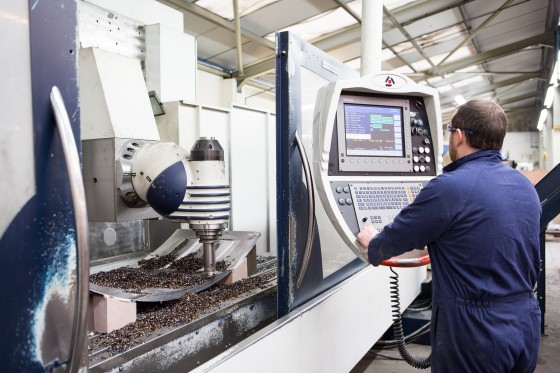
The solution was in changing to Delcam PowerMill, now used to keep all ten CAM units busy with only three seats of the software. “We have effectively doubled our programming capacity with the three seats of PowerMill because the software is so much easier to use,” says Mike Parker, managing director at G. Parker.
Most of the staff are time-served toolmakers with a wealth of aerospace knowledge, and their skills and expertise are needed on almost every job. In addition, G. Parker puts a strong emphasis on encouraging direct interaction between staff and customers. “We have built up a detailed knowledge of our customers’ equipment so we can make tooling that will be easy for them to install and efficient for them to use,” says Parker.
Craig Cooke, Production Manager, had used an alternative CAM system for all his working life but hasn’t found anything that PowerMill can’t do. “All four people that we have trained in PowerMill have been very motivated. Of course, introducing new software has seen some difficulties but nothing insurmountable,” he said.
A key benefit of PowerMill for G. Parker is that it is purely a machining package. “It is much simpler to exchange knowledge between the different users because it is so much easier to use,” says Cooke. “Stock models are much easier to use in PowerMill so we are able to reduce air cutting and shorten machining times with rest machining. We had always struggled with creating undercuts but programming for disc cutters is extremely quick in PowerMill. The surface finish we get now is very good; it is extremely smooth with no faceting. This has reduced polishing time by an average of 20%.”
The productivity boost from introducing PowerMill has come at an important time for G. Parker. “Business is pretty good,” says Mike Parker. “We already have enough projects lined up to make 2016 a better year than 2015. We have plans to add more five-axis machines as they always seem to be fully booked and we will be recruiting two more apprentices. Extra training, including more PowerMill courses, is also planned for the existing staff to make them more flexible so we are able to take on more projects.”