New models for fluid structure interaction and thermal stress evolution lead a wide variety of updates.
The new version of Flow-3D computational fluid dynamics software from Flow Science provides two new computational models, symmetrical multiprocessing for faster computation, and a variety of improvements and fixes to existing components.
New to Flow-3D Version 10.0 are two CFD models. Fluid structure interaction and thermal stress evolution models simulate and analyze the deformations of solid components and solidified fluid regions and resulting stresses in response to pressure forces and thermal gradients. The models use a combination of conforming finite-element and structured finite-difference meshes and have broad applications across industries.
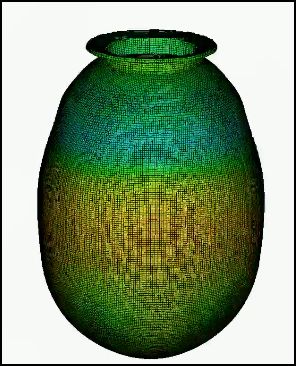
Fluid structure interaction describes fully coupled interaction between fluid and solid using a finite element approach to model stresses and deformations in solid components, in response to pressure forces from the surrounding fluid, thermal gradients, and specified constraints. Currently, the model is limited to small deformations.
Thermal stress evolution describes the evolution of stresses and deformations in metal during cooling. Stresses are simultaneously computed in the mold and in solidifying metal with simple options for the interaction between them.
“The addition of the fluid structure interaction and thermal stress models give our users even more sophisticated and fundamental numerical modeling capabilities,” says Michael Barkhudarov, Flow Science’s Vice President of Research and Development.
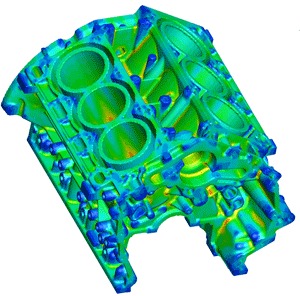
A variety of improvements were made to existing models:
Waves—A new solution added to the surface wave generator model, based on Fourier series, extends the wave generation capability to all periodic non-linear waves. Tsunami waves can be simulated using a solitary wave model, and a random wave generator creates realistic wave conditions at open sea. A periodic wave profile can be used to define fluid initial conditions to speed up the approach to a steady-state wave pattern.
Wind—The definition of the wind shear at the surface of a reservoir has been extended to include time-dependent conditions.
Shallow water—The shallow water model now includes separate models for laminar and turbulent flows, and a way to define Earth rotation by simply defining the latitude. The additions extend the use of the model to large scale flows.
Mass and mass/momentum—The mass and mass/momentum source models have been redesigned so that properties, such as fluid type, density and temperature, mass or volume flow rate, can be defined for individual sources, greatly enhancing the capabilities of the model.
Moisture drying—Two models are now available to describe the evolution of moisture in porous components. A simpler, isothermal model is suitable for sand molds and cores during filling and solidification. The second option uses a more sophisticated two-phase liquid/gas model and is designed to simulate the drying process of porous materials such as paper, fabric and sand cores.
Iron solidification model—The cast iron solidification model describes eutectic and near-eutectic solidification of cast irons, coupled with the Simple Solidification Shrinkage model. The formation of austenite, graphite and carbide phases is also predicted.
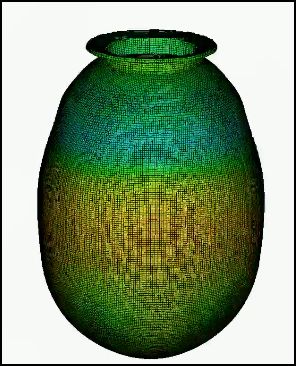
Flow-3D Version 10.0 also includes new symmetrical multiprocessing (SMP) parallelization for almost all models. SMP allows the software to take advantage of all processors on multi-core CPUs.
Flow-3D Version 10.0 is now available to existing customers under maintenance contracts. More information at the Flow-3D product page.