The small maker of high-performance cars for recreational racing created a new suspension system and improved aerodynamics with a team of four.
Recreational auto racing is a small industry where enthusiasts and manufacturers form more of a community than is possible in professional racing. Palatov Motorsport of Portland, Oregon has become successful in recreational racing by designing and building both built-to-order high-performance racecars but also designing components for custom car applications. Founder and managing director Dennis Palatov says his small operation wouldn’t be possible without SolidWorks; “It works the way my brain works.”
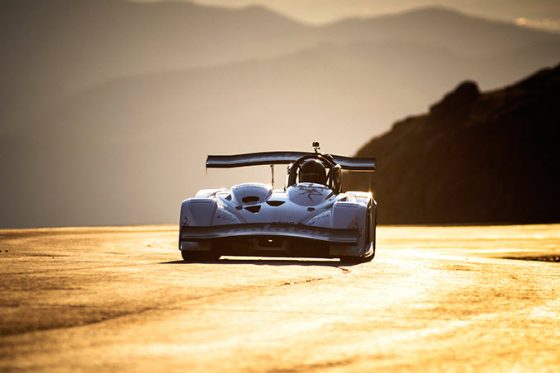
Trained as a mechanical engineer, Palatov designed computer enclosures for a living before starting his manufacturing company. In 1995 he chose the young SolidWorks over competing brands of 3D design tools, which in those days required specialty workstations instead of a Windows-based PC. When he moved on, he stayed with SolidWorks.
“I design complete cars, featuring tight tolerances, from scratch by myself, and we assemble the cars with a team of four,” Palatov says. “Most specialty cars are developed by teams of 20 to 30 people or more. We would not be able to do what we do at Palatov Motorsport without SolidWorks.” The company added integrated SolidWorks Flow Simulation computational fluid dynamics (CFD) analysis software in 2012 to optimize aerodynamic performance.
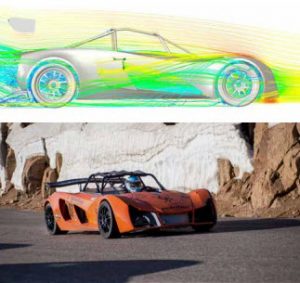
Recently Palatov Motorsport used Flow Simulation to help design the D1PPS, a car built to compete in the Pike’s Peak International Hill Climb in Colorado. It is 12.42-mile race to the top of the 14,110-foot peak, with 156 tight turns. The design team ran flow analysis inside SolidWorks, then compared the results to data obtained by physical testing. “We found a 98% correlation between SolidWorks Flow Simulation results and what actually happens, which gave us confidence to rely on the software to improve aerodynamic performance.” The team maintained 400 pounds of downforce on the car at 100 mph, using CAE results to optimize distribution of forces.
Palatov Motorsport has also created a new patent-pending suspension design which eliminates the need for anti-roll bars and aero-assist third springs in performance racecards. Palatov started by defining relationships and equations in a sketch, then moved to SolidWorks for full design and analysis. “By changing key dimensions in a series of progressive iterations, I was able to quickly optimize the design to achieve the desired performance.”
A Day with Palatov Motorsport in the Eastern Oregon desert. (Source: Minute Rice Channel)