The refined module will ship in the next release of PowerShape, due in August.
The new version of Delcam PowerShape—due for release in August—includes an upgrade to the Solid Doctor module for data repair. PowerShape offers integrated surface, solid, and triangle modelling tools, primarily for manufacturing engineers and CAM operations.
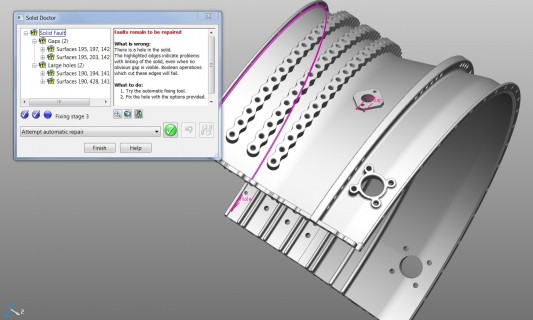
Solid Doctor offers a set of tools for the repair of CAD models from all sources, including IGES, STEP and native Catia files. Delcam say it can be used for all the common problems found when translating low-precision and incomplete data, including gaps and overlaps between surfaces, or duplicated and missing surfaces.
The changes are not obvious at first glance, says PowerShape Development Manager, Ian Watkins. “Most of the changes have been in the background to make the automatic repair tools faster and more robust. We have also made the recommendations clearer on the actions that need to be taken to solve the different types of problem.”
The refined Solid Doctor uses a combination of automatic data repair tools together with the surface creation and editing options available from PowerShape. Delcam says the combination means simple repairs can be carried out quickly and easily, while more complex problems can be overcome by deleting and replacing the existing surfaces within the model.
Steps to the cure
The first stage in using Solid Doctor is to analyze the model to determine the extent of any inconsistency issues in topology or geometry. These errors are labelled on the model and divided into separate categories. For each category or class of inconsistency, Solid Doctor recommends the most appropriate course of action, including a possible automatic fix.
The user then applies the automated repair sequence. Each corrected issue has its label changed from red to green as it is repaired. The repairs can be inspected individually to ensure that the results are as required or the whole model can be checked again to highlight any further inconsistencies.
The second repair stage involves using Delcam’s trim region editing tools to correct larger issues that require manual repair, such as mismatches between the edges of the various surfaces within the model. These include direct editing options for the trim boundaries, which allow very quick and flexible adjustment of the surface edges to overcome errors in the model.
For more serious problems that remain, it will usually be necessary to generate replacement surfaces in the affected area. This can be done using PowerShape’s Smart Surfacing technology. The user deletes the existing surfaces and sketches around the area to be repaired. PowerShape will then analyze the boundary and suggest the most appropriate type of surface to fill the space. Tangency can be maintained with the surrounding surfaces if required. If the user is not happy with the initial selection made by the software, the software allows for running alternative solutions until satisfactory results are achieved. The repaired surfaces are incorporated back into the solid model automatically, and the process continues until all inconsistencies are resolved.