ImpactXoft played an important role in the development of feature modeling in mechanical CAD. Their work has influenced the current generation of design tools from vendors such as SpaceClaim, Siemens PLM, Dassault Systemes, and Autodesk. In an archive article from the February 2007 edition of Engineering Automation Report, Steve Wolfe explores the history and the technology.
By L. Stephen Wolfe, P.E.
Engineering Automation Report, February 2007—In the opening session of Autodesk University on November 28, 2006, Kevin Schneider, whom Autodesk has dubbed a technology evangelist, demonstrated a new kind of functional modeling capability running in the Inventor CAD software. It was a triumphant moment for Attilio Rimoldi, Gian Paolo Bassi, and the dozens of engineers at ImpactXoft who struggled for seven years to develop a new way to apply features to CAD solid models. Although their company is no longer in business, the technologies they conceived have been adopted by the two largest CAD companies: Autodesk and Dassault Systèmes. CAD customers will benefit by having the use of tools that might otherwise have been lost.
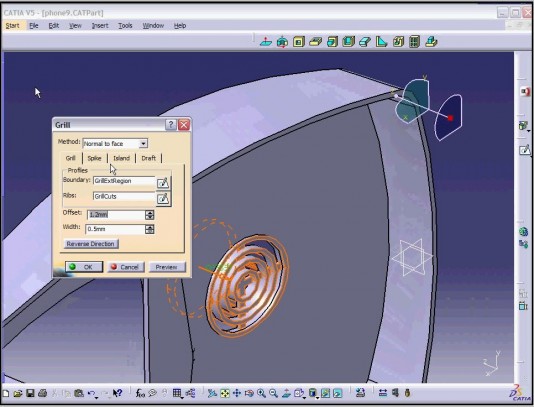
ImpactXoft was founded in 1999 to develop CAD software that incorporated two new technologies: functional modeling and simultaneous designer collaboration. ImpactXoft’s functional modeling features create geometry that might require multiple features in a typical CAD program based on the methods pioneered by Pro/Engineer. For example, crafting a lip around the edge of a plastic casting might require multiple cuts and sweeps in a conventional CAD program. With ImpactXoft’s IX Design, a separate lip function does the job in one operation.
A second important characteristic of ImpactXoft’s functional modeling is that features go together without regard to the order in which they are created. Functional features enable plastic castings to be created faster and with fewer features than conventional CAD systems require. These properties also make functional models easier for others to modify when the need arises. Feature failures also are much less common.
Because the order in which features are applied is immaterial, functional features allow two or more designers to work simultaneously on the same part. For example, a stylist can shape the exterior of an electronic case while an engineer applies ribs and bosses to the circuit boards within. Parametric Technology enabled simultaneous collaboration with its Wildfire release of Pro/Engineer. But the technology hasn’t caught on with customers in part because two people working simultaneously on a history-dependent model will drive each other nuts.
Aborted launch
Although ImpactXoft hatched interesting new concepts, its original implementation was flawed. The first version of IX Design had a cumbersome control set, an archaic look, and inadequate drafting tools. When it didn’t sell, ImpactXoft cut a deal with Dassault Systèmes to employ the CAA toolset for CATIA V5.
Using the CATIA tools, ImpactXoft wrote an application embedded in CATIA to facilitate the design of plastic castings called Functional Molded Parts (FM1). Large CATIA customers that make consumer products have embraced the product enthusiastically, according to Jacques Leveill, president of the CATIA group.
ImpactXoft also used the CATIA toolset to write a complete CAD package for sale under its own label. It included CATIA V5 tools for drafting and data import and export. Drawings and models produced by the system were file-compatible with the CATIA V5 software distributed by IBM so they could be used with other CATIA applications such as numerically controlled tool programming and finite element analysis.
Rimoldi said that conflict with IBM’s dealer channel inhibited sales of IX Design V5. Revenues from the sale of FM1, sold as an extra cost application for CATIA V5, and a similar OEM agreement with Toyota Caelum (a Japanese CAD company spawned by Toyota Motors) weren’t sufficient to pay ImpactXoft’s bills.
Phoenix from the ashes
ImpactXoft ceased operation late in 2005. Dassault Systèmes agreed to license ImpactXoft’s technologies and patents on a non-exclusive basis for a fixed sum of money. The CATIA group will therefore be able to continue supporting and developing FM1 and similar applications indefinitely.
ImpactXoft signed a similar technology-sharing agreement with Autodesk in November 2006. Some of ImpactXoft’s former developers built software into Inventor that enabled the demonstration at Autodesk U. much as they had built functional modeling into CATIA V5.
Autodesk declines to say when it will release a version of Inventor that incorporates ImpactXoft’s functional modeling. An Autodesk marketing manager wouldn’t even acknowledge that the source of the software demonstrated at Autodesk University was ImpactXoft.
Informed sources say that ImpactXoft’s code will not be in the Inventor release expected in the spring of 2007. That means Inventor customers can’t expect functional modeling of the sort found in CATIA V5 until spring 2008 at the earliest.
Whether functional features turn out to be a boon for Inventor customers who design molded parts will depend on how well Autodesk implements them. To be useful, functional features must apply all the details that customers require, such as rounds and draft angles.
Caveats aside, Autodesk should be applauded for embracing functional modeling. It has recently applied the term to its ”design accelerator,” a capability acquired with the Germany company Mechsoft that enables models of assemblies such as gears, shafts, cams, belt drives, and fasteners to be generated automatically from functional specifications. The addition of ImpactXoft’s technology will further extend the depth and richness of this concept. Autodesk also has the opportunity to employ ImpactXoft’s collaboration technology, as does Dassault Systèmes.