Engineering simulation and analysis is getting a major hardware upgrade, due to the rise of general purpose graphics processing units. As CAE companies adjust to the new world of parallel computing, impressive speed gains are achieved.
The 3rd annual Nvidia GPU Technology Conference in September was organized to show off R&D in the fast-growing world of parallel computing using graphic processing units (GPUs) to share the load with CPUs. This “democratization of parallel computing” (as Nvidia CEO Jen-Hsun Huang calls it) is proving to offer profound benefits in a wide variety of fields where progress has been hampered by limits to computational horsepower.
One of those fields is engineering simulation and analysis, also called computer aided engineering (CAE). For years CAE has been left to the tail end of product development, a process conducted by specialists to prove the validity of a particular design. The formulas were so complex as to require enormous processor time, or access to supercomputers, or both. Recent improvements in desktop computer performance, such as the Nehalem generation of Intel Xeon processors, has opened the doors to accessible high-performance computing (HPC) for engineering; GPU computing promises to kick the doors off.
Several companies, from market leaders to incubator startups, demonstrated GPU-based simulation solutions at the Nvidia conference. Nvidia gave a few minutes of the opening day main stage presentation to simulation market leader Ansys. Before the end of the year Ansys will release an update to Ansys Mechanical that can harness Nvidia GPU and CUDA (the Nvidia GPU programming language) to accelerate performance. Dr. S. Subbiah, VP of Global Business Development at Ansys, says they tested the new GPU-based simulator on a dozen different customer situations, and found an average 2x improvement in processing time. Problems that were taking a week to run before were now being solved in 2.5 days.
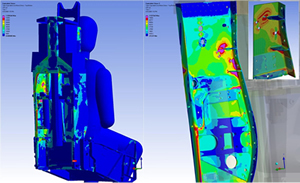
Such drastic improvement does more than shorten development time, Subbiah says; it makes it possible for simulation to lead product development instead of just test it. The result for both the giants of industry and small production shops is the “democratization of design simulation.” Simulation can become more multi-disciplinary, as it becomes practical to test the interaction of mechanical and electrical systems as well as external forces in one unified process.
The Simulia division of Dassault Systémes is also working to implement GPU-based simulation. Simulia’s Luis Crivelli says the company’s Abaqus CAE software scales “very well” to multi-core CPUs, but the real excitement will come as they finish tweaking the code for GPU computing. “The democratization of HPC excites us,” Crivelli says. “We have great expectations for the future of general purpose GPUs for simulation.”
As usual in emerging technologies, some of the most interesting research is coming from start-ups and university labs. Prometech Software of Japan presented its ParticleWorks software at the Nvidia conference, a particle-based approach to CAE. Standard approaches to simulation start by computing a mesh—an unstructured grid that defines the shape of a solid model. Data about the model is then calculated on the mesh and stored in relation to it. Prometech has been developing a “meshless” method of simulation it calls moving particle simulation (MPS). The data is stored on the particles. It is suited to situations with large deformations, free surfaces, or incompressible fluids in interaction with solids.
Prometech presented the results of two benchmark simulations at the Nvidia conference. In both cases, the ‘before’ was an Intel quad-core i7, the ‘after’ was the same unit with an Nvidia GPU. The first benchmark was an automotive collision detection simulation. The performance gain was 8.2x faster using GPUs. The second was a chemical mixing simulation for an automobile tire company and its chemistry partner, testing mixer torque in a high viscosity environment. The performance gain was 9.3x faster. To put these results in perspective, a 2x performance means the process time was cut in half.
Prometech says the performance gain is achieved through:
- Optimizing the iterative solver for particle simulation
- Optimizing the particle interaction for GPUs
- Holding the interaction list created by collision detection by use of large memory consumption and saving a record of all memory transactions and floating-point operations.
Hurdles remain
Ansys Mechanical will be the best known manufacturing simulation program to incorporate GPU-based parallel computing when it debuts, and solutions are on the way from other leading vendors. But hurdles remain before all players in engineering simulation and analysis are on the GPU highway. Some simulation algorithms have been highly optimized over the years for use on single CPUs, and the work to move them to parallel computing is not trivial. For example, industry insiders say it might be late 2011 before a vendor offers a GPU-based solution for computational fluid dynamics (CFD), due to the complexity of the path from single CPU to a GPU environment.
LS-DYNA is an advanced multi-physics CAE simulation code used in a variety of industries. Its origins can be traced back to testing atomic bombs. Dr. Robert Lucas from University of Southern California says researchers “have been patiently waiting for years” for GPU technology to reach the point where it could be put to work in LS-DYNA and similar solvers. His current research indicates that approximately 89% of current LS-DYNA operations are suitable for porting to the GPU environment. But, he warns, current GPU technology will make LS-DYNA faster “but not drastically faster.” Explicit solving in LS-DYNA is accomplished with millions of lines of FORTRAN code, versus only “hundreds” of lines for implicit solving. Lucas is looking down the road to projected improvements in GPU technology before the big gains seen by researchers like Prometech are realized.
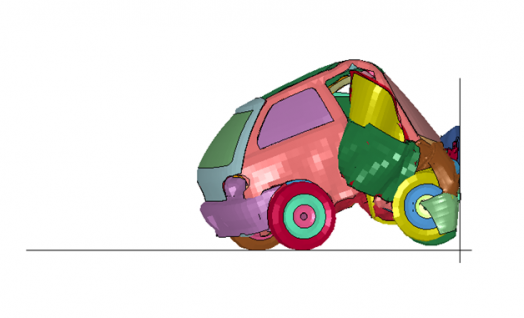