The work must go on; but life will never be the same.

There probably is no good time for a pandemic, but this particular Coronavirus shutdown hits the construction industry at a particularly bad time. Spring means construction, but for most of the U.S. construction was shut down in March and April, and just now ramping up in May.
However, when it comes to infrastructure projects, the work has been going on in many states in spite of the Coronavirus pandemic. Crews are taking advantage of fewer cars on the road to keep projects going. This is true in most states and some, notes Bentley Systems’ vice president civil infrastructure, Francois Valois, have expanded their projects to take advantage of the improved road access including Minnesota, Florida, and Arizona.
But, even as projects have continued, the rapid shift to remote working has been challenging in the AEC industry. The crisis has demonstrated where there are problems, but it also has accelerated the adoption of advanced technology.
According to traditional wisdom, companies that are able to innovate during times of recession are more successful coming out of that recession. Sometimes, in fact, it’s a matter of survival if old approaches are no longer working. The CAD companies universally are preaching this gospel because they want their customers all signed up on subscription, networked and sharing information on common systems. They’ve wanted some form of this for just about as long as there have been networks but customers have been wary of being locked into systems.
Those attitudes are changing rapidly and that’s due in no small part to the increased use of remote conferencing tools to allow work from home. Zoom and other easy web conferencing tools are so easy that it’s bringing the technology averse into the next era of networked communication. We’re seeing the CAD companies offer free access to cloud-based tools for all sorts of jobs. For instance, PTC is offering free access to its AR remote assistance and maintenance tool Vuforia Chalk; Graebert has offered access to its Kudo online CAD tools for drafting and is learning how and where people use online tools; Autodesk is offering free access to its cloud tools; to celebrate Project Wise 365 Bentley is offering free access through the summer. There is momentum.
The pandemic has hit at the same time that tools for collaborative workflows have come into their own becoming easier to adopt at the same time.
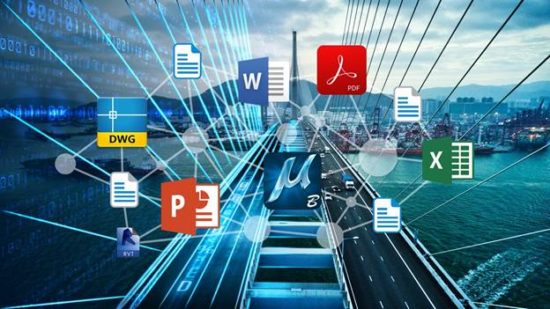
At its annual Year in Infrastructure conference, Bentley Systems wholeheartedly adopted the digital twin concept for AEC and infrastructure projects. Bentley introduced the iTwin Services partner program to enlist outside developers to help it add to the development of digital twin technology. The company wants to be able to manage data as the Internet of Things comes to buildings and bridges with embedded sensors and networked systems.
In addition, the company has been building an edge through its use of open technologies, and standard platforms. For instance, Bentley has enthusiastically partnered with Microsoft to build on the Microsoft 365 architecture. The company is using Microsoft Teams for conferencing and project communication. As an aside, Siemens, a frequent Bentley Partner, also supports Microsoft’s technology for collaboration and communication.
What’s at work here is not just an attitude of why re-invent the wheel, but also the adoption of an accessible platform for companies. In design and engineering, most people use Windows-based computers and almost all use Microsoft Office tools for documentation. Microsoft has already built in a framework for collaboration with its Azure cloud, OneNote storage, Teams collaboration tools, and it’s all considerably easier and less expensive to implement than earlier, heavier client/server approaches.
Bentley’s ProjectWise 365 has been built on Microsoft Office 365 as an easy to access option for contractors, small businesses, etc. Admittedly, it’s large companies that are driving BIM, collaborative computing, and cloud resources; but in order for the software to be rolled out into the broader construction industry, there may be many small companies that also need to get added to the system. ProjectWise 365 can make that happen as an ad hoc process. It can be a hybrid setup: onprem and cloud. As Bentley’s Dustin Parkman, VP Project Delivery, told us, the advantage of ProjectWise 365 is that there is a low barrier to entry, but also, it can sale up exponentially connect where appropriate with Project Wise systems.
However, the fast shift to working from home caused by the Coronavirus also highlighted some challenges, or at least calls into question some established ways of working. For instance, engineers and designers, CAD professionals, in general, tend to use workstations tied-in to company networks. In many cases, it was easier for workers to lug home hefty workstations because they were linked to company networks and software licenses. When those workstations got back to the house, it fell to the company IT department to set up users’ home systems as well. VPN networks are still being used in many of these ad hoc situations. However, it is these kinds of situations that are helping make the case for cloud-based approaches.
Also, while companies may say they’ve adopted BIM, sometimes not everyone involved in the project has access to the same resources. In the U.S., there are no government mandates for BIM. It’s a state-by-state situation, which isn’t very surprising right now, given the U.S.’ pandemic response.
SVP Kevin Kornish of AECOM says his company has over 20,000 employees in 300 offices worldwide. He says the company had already enabled remote working for many of their employees so they were able to adapt quickly. They have standardized on ProjectWise worldwide and Cornish says they’ve recognized the need to connect with teams and managers, to have a reliable IT infrastructure, and to be able to access the data related to a project without the limitations of VPNs.
Most of their offices are open, but the majority of their workers are working remotely. “It will be interesting to see the degree to which we continue to work remotely,” he says. But, because the actual work he is doing is with teams who gather together around a design, model, blueprint, or on the site to get closer looks at issues and problems, he thinks many of his colleagues will be eager to get back to work together.
The company actively develops solutions for its projects working with multiple vendors including, of course, Bentley and Autodesk. Cornish sees more opportunities for changing the way people work out on the site where communication has been more difficult. He’s positive that people working in the field on construction will welcome the advances of remote computing and collaborative tools. He notes practices there have to change. His office is using Bentley’s Synchro construction management tool for communication during the construction process.
Andy Kaiyala, Vice President of building development for Lane Construction, identifies some of the same problems that Cornish does. Lane is part of Salini Impreglio, a large company with 35,000 employees in over 50 countries. He says that one of the most important questions in the construction industry is where do I go to find the information I need. He says people can sometimes spend half a day searching for information. Is it in the trailer, on my mobile, or is it in a set of plans in my pickup? He says what’s needed is a single source of the truth, a common data environment.
He notes contractors have different concerns, “we don’t look at a project the same way that a designer or the client does.” He says the concern is “what steps do I need to take to perform this task. He identifies Bentley’s Synchro as a promising tool, as he reviews Bentley’s development plans. He says that contractors didn’t have the ability to break down the model according to tasks—the work breakdown structure (WBS).
Additional insight into what’s actually happening in the construction industry has also come to us from CAD consultants and developers nCircleTech who are based in Pune, India but have projects worldwide. In a recent webinar, Varun Bhartiya, nCircleTech co-founder, and CEO, asked construction experts Tom Cuneio, founder of 3DIQ, and Stephan Jones, from AECOM in London, about the ways in which they see the AEC industry-transforming to adapt to the Coronavirus pandemic. Jones, interestingly enough, was one of the founders of Synchro before it was acquired by Bentley. What he has come to appreciate is the difficulty of getting any technology, no matter how worthy, integrated uniformly for large companies.
Bhartiya says it’s already very clear that the Coronavirus will transform the world. Its negative effects are obvious in terms of financial losses. Bhartiya quotes Goldman Sachs economists who predict US GDP will plunge 34% while the unemployment will rise to 15%. In fact, the Bureau of Labor Statistics says the rate of unemployment in May is at 14.7%. In the UK, Bhartiya says over 65% of projects were closed during production and already are costing as much as an astounding £104 billion.
Both Cuneio of 3DIQ and Jones from AECOM note that in many cases, the necessary technology is in place, or is readily available. What they’re learning during the pandemic shutdowns is that it’s not evenly distributed, to paraphrase William Gibson’s observations on the future.
Cuneio says an important thing to remember through all this is that businesses rely on relationships. “If we’re going to be able to interact and have social distancing if it’s not just for today, then we need great digital content. Cuneio’s company specializes in masonry and he’s developed tools to design projects and manage the supply chain. He’s often working directly with suppliers who are telling him now that they need new ways to get their product in front of the community. They’re asking, “Are there ways we can build virtual showrooms.”
He says, “the pandemic has taught us the need for flexibility. We need to able to scale up and scale down according to need.”
Jones, who works for AECOM in London, says the Coronavirus has accelerated the transitions his company was already moving on, albeit slowly. For instance, he said, they have been pursuing a migration away from network drives towards a common data environment. He says, “For the last 3 years, we may have been ticking along at 5% but within two weeks we exceeded 75% of integration.”
Cuneio seems a similar trend. “The first step,” he says, “is to look at the technology we already have that we’re not integrating efficiently and improve implementation.” What they’ve seen is that as they take advantage of the technology they have, they see new technology grow up around it.
Another lesson learned from the virus is the value of sprint approaches, says Jones. “The advantage of moving fast is that it gives you a point of reference, you can evaluate the shift in technology,” and with past experience so close in the rearview mirror it’s easier to make assessments and adjust course.
Tom Cuneio said that so much of this had been made clear by the current crisis. “Covid-19 has the effect of a mandate.” And, in order to get up and moving rapidly, he added, “we need good data.” Looking ahead, Cuneio sees the potential for more crises, “we’ll see more mandates,” he anticipates the creation of data reservoirs, which will be great for the construction industry.
In this, he echoes Microsoft’s call for more data and more open data for all developers. “We’re on the verge of a great time of data,” says Cuneio.
So, okay, they have the technology and they have the will. Now it’s a matter of distribution. There is the issue of Synchro, which, says Jones, is only used in pockets throughout AECOM and is not part of the company’s standard workload. He says they are using the lessons learned and “we are developing a next-gen calculator that fits into our broader core strategy.”
In another example, Stephan says he’s worked with team members who used Autodesk Dynamo for automating tasks. “We have done some amazing things,” he says and engineers are coming up with new ideas for automation all the time, but “we don’t get the return on investment we thought we’d get.” And again, the problem is one of scale. Separate groups are seeing the value of point solutions, but the benefits are not shared.
The same is true of equipment. He notes that AECOM is often the first to buy new techs such as scanners and drones. “We find there are pockets of innovation in our business, but we don’t see a return on investment.” He says it’s common for large companies to fail to amortize purchases across projects.
Jones is optimistic about the future because of the lessons being learned now. He says, for AECOM reorganization, the uptake of BIM 360, fast actions, decisive actions have given the company to take their improvements forward.
How will things be different in the future?
Even before the arrival of the pandemic and lockdown, there has been a trend in construction towards modularization, automation, the use of video for process monitoring. Scheduling tools that are part of Autodesk Construction Cloud and Bentley’s Synchro can help with pre-planning and staging so advance work can be done off-site and fewer people need to be onsite—or they can be on-site for less time. The use of drones and cameras can enable management from afar.
It’s worth mentioning in fact, that in terms of the pandemic and construction, the work is often socially distanced simply because of machinery and the trend towards better planning and the use of sensors on the job as well as for the job is part of the efficiency improvements were already in process but, as Steven Jones noted, the Coronavirus has accelerated the process.
Lessons learned
From these discussions, it seems the construction industry, as it has evolved over the last five years, is prepared to continue work during a crisis but this particular crisis has enabled companies to see what’s working, what’s not working, and what more they have to do.
Probably the number one issue that was repeatedly mentioned was streamlining data systems so information can be found. All companies claim all the time that they have systems in place to manage data but this crisis, which forced companies to suddenly pick up sticks and go home, shows where the friction is and where people were relying on workarounds. The companies cited in this article are the ones that are pretty proud of their performance, but all of them have noted that the crisis has driven further innovation.
What’s also become very evident is that everyone has to join the party which favors easy to implement applications over custom-built systems. The most advanced technology will be the technology that’s easiest to learn, adopt, and roll out.