The University of Florida researchers are building stronger, more comfortable and less expensive implants with a soft silicone printing process.
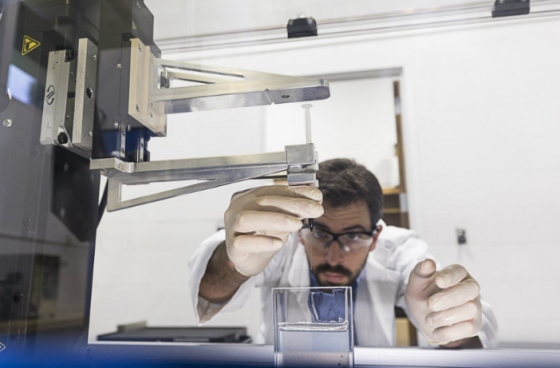
Researchers from the University of Florida have devised a new process for 3D printing in soft silicone to manufacture medical implants like ports for draining bodily fluids, implantable bands, balloons, soft catheters, slings, and meshes.
Silicone is 3D printed into the micro-organogel support material. (Source: University of Florida)
Silicone is 3D printed into the micro-organogel support material. The printing nozzle follows a predefined trajectory, depositing liquid silicone in its wake.
Customary medical devices are usually molded, which takes days or weeks to create customized parts to fit an individual patient. The 3D printing method cuts down build time significantly. Moreover, the 3D technology allows for extremely small and complex devices, such as drainage tubes containing pressure-sensitive valves to be built in one go, too complicated to create using traditional methods.
The new 3D printing method also could pave the path for new therapeutic devices that encapsulate and control the release of drugs or small molecules for guiding tissue regeneration or assisting diseased organs such as the pancreas or prostate. The cost savings would be substantial for both customer and the maker.
“Printable Organs and Tissues” is a project Thomas E. Angelini and co-workers have been working on for several years. Their work as “UF Soft Matter” led to finding a revolutionary way to manufacture soft materials using 3D printing and microscopic hydrogel particles as a medium.
The difficulty faced by researchers was in 3D printing material; the previous water-based granular gel materials were incompatible with oily “inks” like silicone. It was like mixing water and oil. The problem was solved with oil-based microgels making 3D printing easier and durable.
Functioning of a reservoir using a 3D printed silicone valve. (Source: University of Florida)
Water is pumped from one reservoir to another using a 3D printed silicone valve. The silicone valve contains two encapsulated ball valves allowing water to be pumped through the valve by squeezing the lower chamber. The silicone valve demonstrates how this 3D printing method can be used to create multiple encapsulated components in a single part — something that cannot be done with a traditional 3D printing approach.
The research team foresees manufacturing human organs and tissues using 3D bioprinting technologies within a decade.
Other members of the UF Soft Matter team are Tapomoy Bhattacharjee, Samuel Hart, Christopher P. Kabb, Kyle D. Schulze, Indrasena Chilakala, Brent S. Sumerlin, and Greg Sawyer.
What do we think?
As 3D printing and medical technology advance, it will soon be possible to construct human tissue in a lab, implant it in a patient and watch it grow into the body. The process is called tissue engineering, one of the more interesting new technological advances medical researchers have made in the medical 3D printing.