Creating and editing Class A curved surfaces to SolidWorks models simplified design workflow.
nPower has released an update to its PowerSurfacing line of add-ins for SolidWorks which improve the ability to create complex and aesthetically pleasing surfaces inside SolidWorks assemblies. Power Surfacing is a SubD (Subdivision Surfacing) based organic modeling tool for SolidWorks based on the Solids++ modeling kernel.
PowerSurfacing and PowerSurfacing RE (reverse engineering) now offers full support to create and edit surfaces while in Assembly mode. There are also additions to its macro capability, new methods for creating SubD surfaces, and more complex use of constraints.
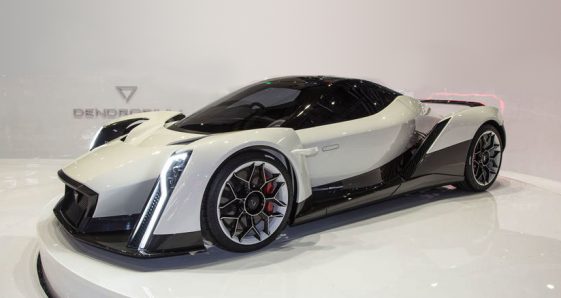
Assemblies: Power Surfacing now fully supports the SolidWorks Assembly modeling environment. It is possible to create and edit Power Surfacing features while in an assembly, and to import reference constraints from other parts in the assembly.
Macro Feature: Power Surfacing bodies are now macro features, which means they behave like typical SolidWorks features. Users can create multiple Power Surface bodies in a single part. Power Surfacing bodies will now automatically update as “standard” features in the feature tree. When a Power Surface body in the feature tree is updated, it will automatically trim and sew the result (and make it into a solid body if it is solid).
Conversion options: Version 4 introduces advanced control over the process for converting Power Surface geometry into SolidWorks bodies. In addition to the typical subdivision levels, it is possible increase the level of refinement, controlling the quality and accuracy.
New surface workflow: A new surface creation mode allows users to extend and shape surfaces on the fly. There is also a new workflow for creating geometry from sketches.
G2 & Offset constraints: G2 constraints create curvature continuous constraints with other geometry, providing a smooth transition and high quality surface continuity. Offset constraints provide great flexibility in creating geometry constrained to an offset from a surface.
PowerSurfacing RE for reverse engineering
PowerSurfacing RE is a second tools for reverse engineering scanned meshes, other meshes, or SolidWorks geometry. nPower says the 4.1 version automates many of the most difficult reverse engineering operations.
Quad Wrap: The Quad Wrap tool automatically wraps a SubD / Power Surfacing mesh around a scanned mesh to retopologize it.
Smart Fill: Smart fill automatically fills in an area (with a quad mesh), while constraining to the reference mesh.
Edit reference mesh: New tools speed up the process of preparing a scanned mesh.
Accelerated face painting: Paint a whole set of faces onto a reference mesh in just a few clicks.
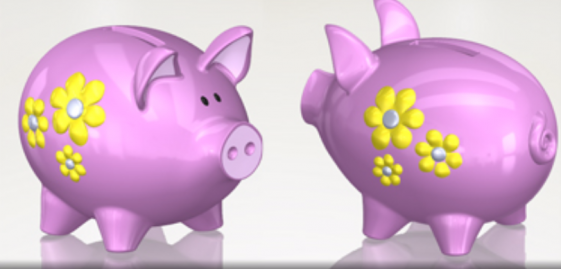
What do we think?
Adding PowerSurfacing to SolidWorks is much cheaper than buying a seat of Catia, which is the other way to have a Class A curves workflow inside one CAD environment. Subdivision Surfacing is becoming more recognized as a useful adjunct to traditional CAD modeling; the PowerSurfacing line makes it easy for SolidWorks uses to have their curves and keep their existing workflow.