Spatial details its latest plans at its 2022 3D Insiders’ Summit.
There is a group of companies and organizations that operate largely under the radar, and that if it were not for them, we would not have the kind of progress in CAD software we have seen over the decades. These companies have names like Spatial (a division of Dassault Systemes), Open Design Alliance, C3D Labs (Ascon), and Siemens; they write the toughest CAD programming code known on planet Earth: geometric kernels.
Kernel code is at the core of all 3D CAD systems. It ensures that solid modeling and surfacing operate precisely, that data between CAD systems translates accurately, and that constraints work at all. In competing with one another, these companies add bonuses to make it easier for CAD programmers to add functions, such as flattening sheet metal automatically or finding curves at the intersections of solids and surfaces.
Spatial is special in being the first company to commercialize a solid modeling kernel, ACIS, developed in the late 1980s in England. Today, it is used by 400 firms. Some CAD vendors, however, built their own kernels, such as Granite by PTC, CGM by Dassault, and ShapeManager by Autodesk, the latter having based its code on ACIS.
Spatial at 33
After 33 years, Spatial has amassed a significant collection of software based on three core products: 3D ACIS Modeler, CGM Core Modeler, and 3D InterOp.
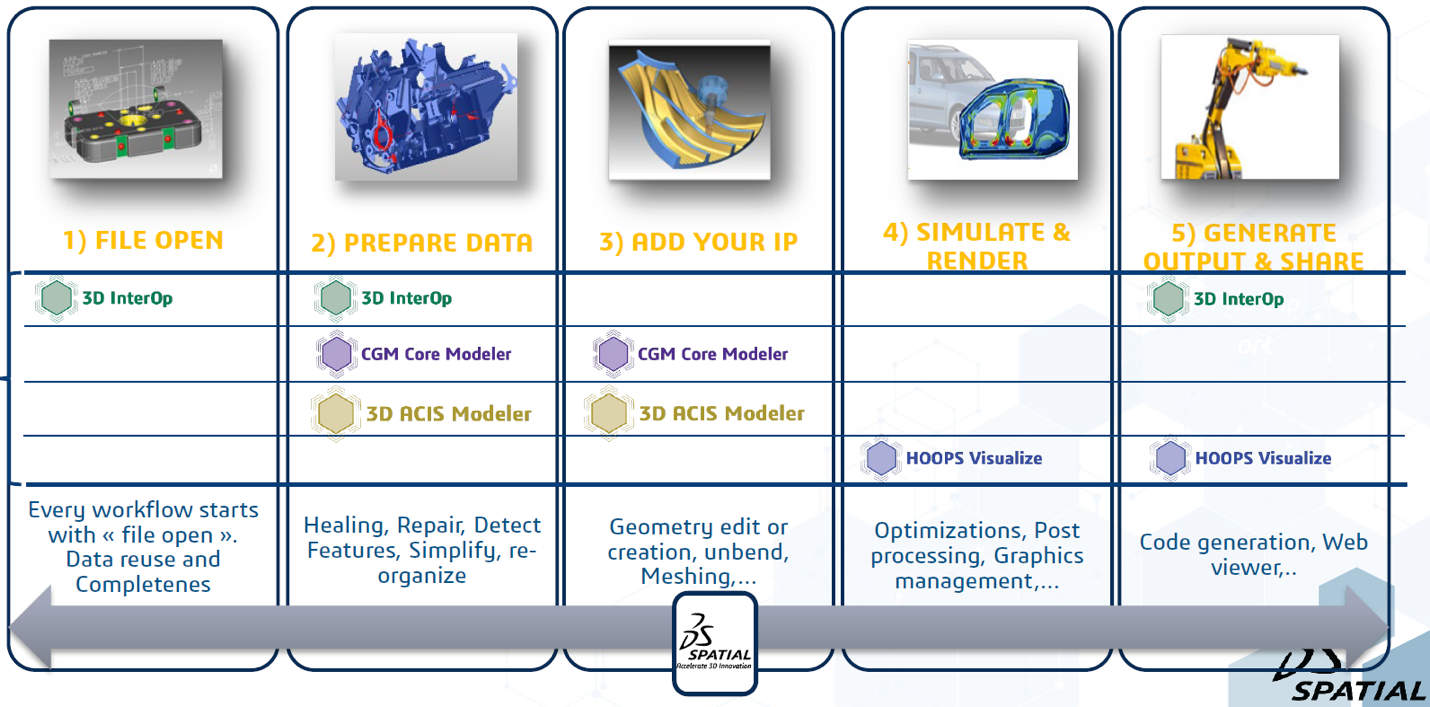
CGM comes from the parent firm Dassault, which tasked Spatial with turning the kernel (used by Dassault’s Catia 3D modeler) into components that can be licensed by others. Stripping out parts to sell as individual modules is a long-term job, and Spatial has been at it for a decade. Today, about two-thirds of Spatial’s 400 customers use ACIS, while one-third use CGM. (The company does not give out any other performance metrics.)
3D InterOp (interoperability) is a data translator that reads and writes many 3D mechanical CAD file formats, as well as DWG/DXF.
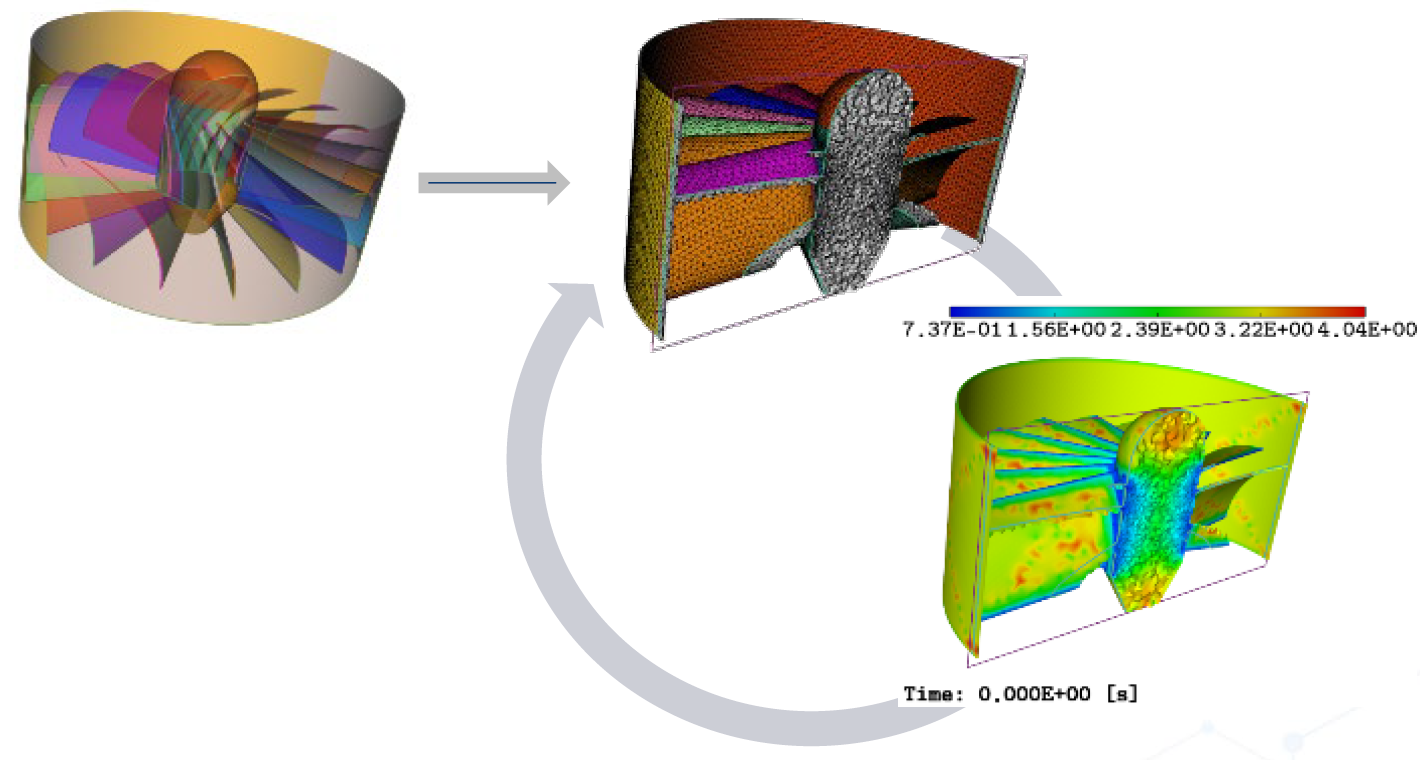
In addition to the big three, these other modules can be licensed separately:
- 3D BIM InterOp translates architectural formats like IFC and RVT; developed in conjunction with Open Design Alliance.
- 3D Precise Mesh generates meshes from solid models in advanced finite element analysis; it is based on MeshGEMS, which Spatial recently acquired with the acquisition of French company Distene.
- AGM (applications graphics manager) assists programmers with templates and coding workflows.
- CDS (constraint design solver) constrains the geometry and dimensions of 2D sketches and 3D parts, and checks for interferences.
- CGM Defeaturing removes unnecessary features for simulation or for hiding IP (intellectual property).
- CGM Polyhedra combines hybrid (mixed) b-rep solid and polyhedral mesh editing.
- CGM HLR (hidden line remover) removes hidden lines for visualizing 3D models.
- HOOPS Visualize generates images from data; it is licensed from TechSoft 3D.
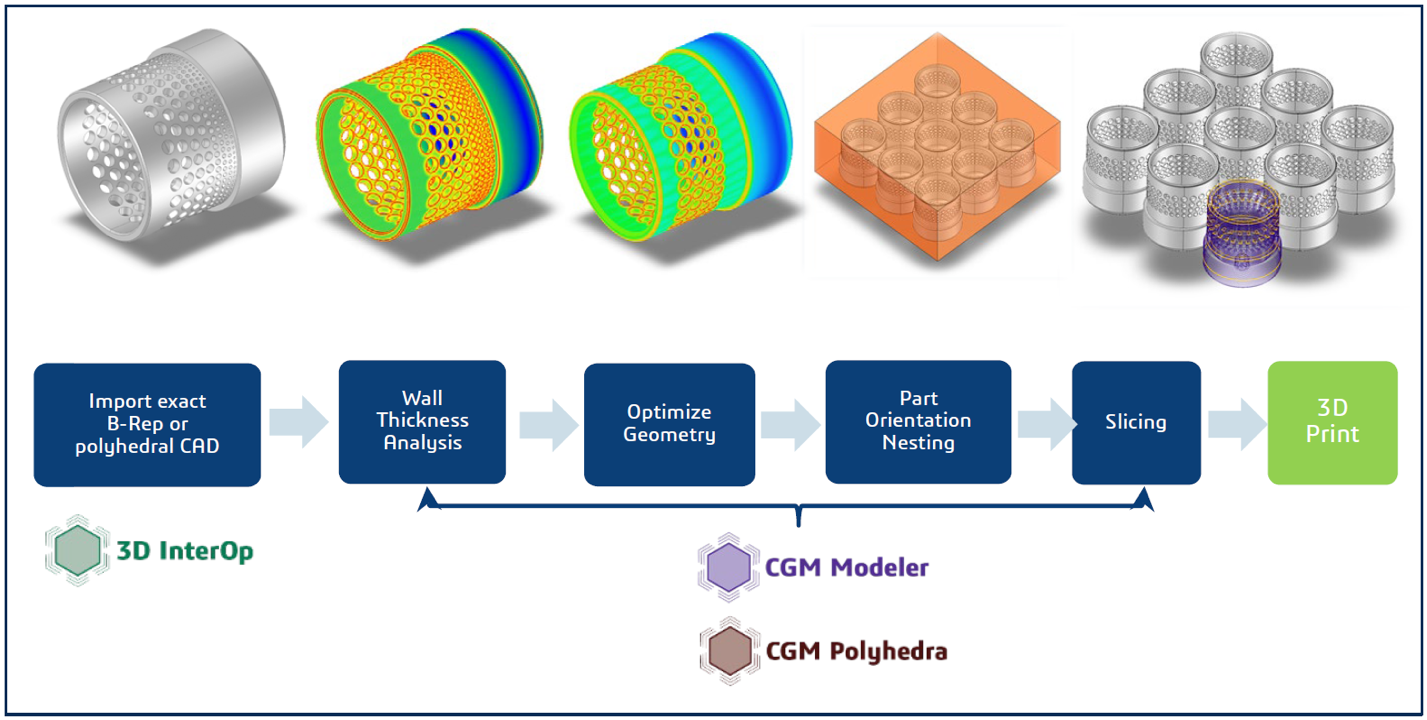
The names prefixed with “CGM” were sourced from Dassault’s CGM modeler; some also work with ACIS. For instance, Spatial expects CGM Polyhedra to be integrated into ACIS by 2023. Although CGM has more capabilities than ACIS, Spatial does not recommend switching from one kernel to another, as that can prove to be too disruptive.
What’s new for ’22
Spatial last month held its 2022 3D Insiders’ Summit for customers who are programmers, detailing its road map for the coming year. As this was the first in-person event since the onslaught of COVID-19, the conference room in Munich was nearly full—much to the relief of conference organizers—as people sought again to be with people.
Much of the day was spent on the capabilities of InterOp. There is, by the nature of the beast, a delay between a CAD vendor releasing changes to its file format and a translation company updating its offering. So, Spatial aims to keep the delay down to three months, which is about 2× faster than is common in the industry.
A significant addition to InterOp is PMI (product manufacturing information), which is like dimensioning combined with GD&T (geometric dimensioning and tolerancing) for 3D models. PMI’s purpose is to explain to CAM machines how to make the parts defined by CAD: the materials to use, the types of machining needed, the tolerances (errors in the distance) allowed, and so on. To give programmers a hand in implementing PMI, Spatial will ship IOPMeta in May, a template that makes it easier to write code for importing and processing PMI and geometry.
For the BIM and CFD formats handled by InterOp, the translation program now supports models as wide as 100 km (such as with civil engineering works) and down to 10 micrometers, such as in watch design. In upcoming releases, InterOp will support assembly cuts in NX and Solidworks, interpret kinematics from STEP AP242 files, and read Creo hole patterns. New formats supported by InterOp will include Intergraph’s SmartPlant and PDMS, both of which require the ability to read large data sets.
Analyzing multi-core processing
Spatial reported at the conference on its analysis of multi-core processing. More CPU cores speed up calculations, but not linearly. Increasing cores from one to eight processes do not make calculations 8× faster, but rather 5.5× faster, due to the added time it takes to set up eight streams of calculations and then to reassemble the results afterward.
Going with too many cores can lead to bottlenecks, such as when some bodies have complex shapes (such as splines intersecting planes), which delay other processors that might be handling simple shapes (such as non-intersecting lines). So, they must wait for the processors handling complex bodies to finish their work.
As a result, Spatial says programmers need to evaluate when to use single-core and when to use multi-core processing.
A kinder, gentler Spatial
The theme of the conference was “being a trusted partner.” Spatial realizes it may have been brusque in the past, and so is turning over a new leaf. For instance, the company redefined what the word “done” means: A product is done when it is ready for use by customers. IOPMeta and AGM are new initiatives to help customers implement code more easily and faster into their CAD programs. Spatial now tries to make sure that updates are meaningful across all APIs (application programming interfaces). Also, it has added a dozen specialists to help programmers when they run into problems and who can guide management in determining the best direction for their continuing 3D software development.
Conclusion
To get an idea of the future of the CAD software you use, you would do well to familiarize yourself with the future plans of firms like Spatial. I see a company eager to compete with longtime stalwarts like Siemens and recent upstarts like C3D Labs. While some of its “new” functions merely catch up with competitors (such as extracting zero-thickness median shapes), others are unique advances, like 3D nesting.
Spatial foresees a time when machinists are no longer needed to operate milling machines and in-house experts are no longer required to process simulations. I don’t know how plausible these goals are; I see them akin to Elon Musk’s aim to reach Mars: SpaceX won’t necessarily ever get to Mars, but the dream acts as an incentive for employees to overshoot in attaining a technological goal.