Defines the digital twin.
Last year, the Siemens design and manufacture subcompany that was known as Siemens PLM signaled a major turning point in its ongoing transformation within the larger Siemens megacompany. It changed its name to Siemens Digital Industries Software, which at least freed the company from the albatross of the unpopular term PLM and also integrated the group tighter into Siemens as a whole.
This year, as part of its preparation for its Realize Live conference, the company has made several announcements to signal the progress it has made with its Mendix acquisition, new alliances, and its journey to the cloud. The company is introducing new Xcelerator tools, a new alliance with IBM, and a major lift to SaaS with Teamcenter, but overarching everything is Siemens’ view of the digital twin.
The company also announced a new AI-based tool called Sketch for NX.
Siemens introduced a Sketch tool for mobile some years ago and has appropriated the name and the spirit of that earlier design for this more sophisticated tool that takes advantage of design advances and AI. In parametric design, sketching provides the basic template for a design as it is started and evolves. The name might make the process seem simple enough, but it never has been. The sketch for a parametric design had to be created with a full understanding of how the model would ultimately work and how the product it describes would be built.
This new tool enables designers to get started without pre-defining parameters and relationships. The new Sketch tool uses AI to infer relationships and has built-in flexibility allowing design iteration. It supports imported designs, complex sketches, and works with legacy data.
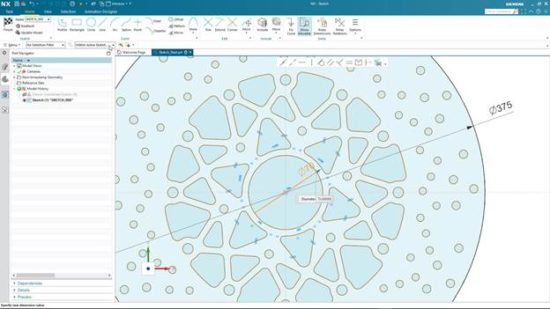
Siemens says that for NX users, 10% of their time may be spent sketching and much of that work is done outside the 3D design tool in order to work out the requirements for the final sketch that would provide the basis of a design. NX Sketch adds intelligence about parametric design requirements to enable designers get to a workable sketch faster and so they can do more of their conceptualization inside NX. In addition, notes Siemens SVP Brenda Discher, Strategy and Marketing, the new Sketch tool helps designers avoid creating an over-constrained situation that’s going to cause problems with the model down the road and will ultimately affect the usefulness of the model within the digital twin.
The new Sketch tool is yet another example of the development going on at the company to enable digital twins. Siemens calls the work it has done to facilitate specific design and manufacturing workflows and tasks Xcelerators.
Xcelerating the digital twin
Mendix is a tool for low-code software development. Siemens acquired Mendix in August 2018 for $730 million and it is using it as a foundational technology for company development going forward. Subsequently, Siemens introduced Xcelerators, packaged technology from Siemens’ Mentor, MindSphere, Siemens Cloud Solutions, and Mendix products to enable companies to digitize their workflows and connect the digital and the physical. They’re offered as the Xcelerator Portfolio.
As an example, the company demonstrated one of their latest Xcelerator tools using Capital, an electrical engineering tool for wiring harness design that’s part of the Mentor family. It’s an example of a purpose-built Xcelerator tool created using Mendix in conjunction with other Siemens tools including NX, Capital, Teamcenter, and MindSphere IoT tools.
Capital, says Siemens, is the leading system for wiring harness design for automotive and aeronautic development. The system can use generative design tools and create a set of variants for every option in wiring for aeronautic and automotive design in the last 10 years, says SVP Martin O’Brien for Siemens Integrated Electrical Systems Business. It can find a wiring design to meet product specifications. It can be simulated, verified, analyzed, and tested end-to-end.
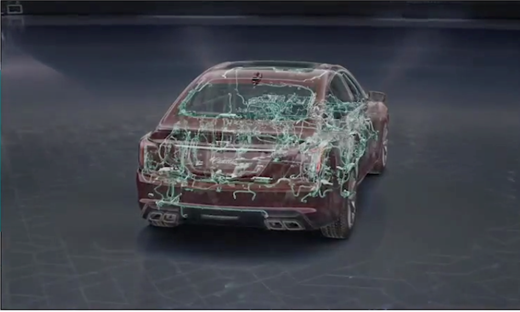
Essentially, Siemens is hoping to build systems of tools that will enable its customers to build their own solutions with a minimum of programming and specialized skills. The goal is for integrated end-to-end model-based design, manufacturing, and service: the digital twin.
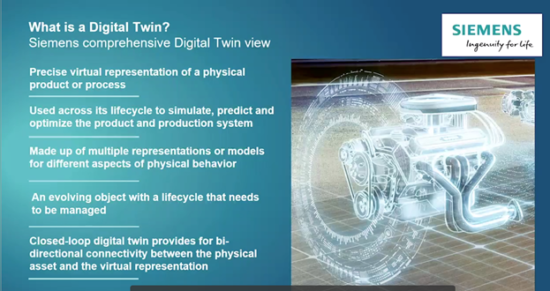
The company emphasizes that customers need to embrace the digital twin because it enables them to make sense of the huge amounts of data connected to today’s product designs as well as enable flexibility and change. This idea of the single digital twin, argues Siemens, separates them from their competitors and Siemens has devoted its development and acquisitions to fill in the blanks for digital twins in their primary industry categories, which include automotive, aeronautic, marine, and machine design to name the largest segments. Siemens also has a large interest in factory automation.
To the cloud
Siemens is also introducing a new version of its information management technology—Teamcenter X, built on Mendix, is a cloud-based tool. It’s no secret that PLM tools can be difficult to install on computers throughout an organization and to get users to use them. Teamcenter X supports Siemens family products including NX, Solid Edge, Mentor electronic CAD tools, and Polarion X for application lifecycle management. It also supports multiple CAD tools and enables a multi-domain bill of materials (BOM) providing access to the digital twin and all the possible components from mechanical, electrical, and software tools. It also includes predictive AI to help users get to the right information faster but best of all, it can be easily adopted with a sign-up to the cloud.
Teamcenter X can be preconfigured for engineering and business solutions and connect teams across disciplines and geographies, all of which make it a good product for SMBs that might not have in-house IT, or maybe challenged to take time off from routine work to get a new system up and running. However, Siemens believes Teamcenter X will ultimately find a home in the enterprise as well and it can be combined with standard Teamcenter implementations. We’re told that some Teamcenter customers are looking at transitioning to SaaS-based PLM for the advantages of easier deployment, consistency, and easier management. SaaS is presenting a path many Siemens customers might take to the cloud.
Siemens also announced the cloud-based Teamcenter Share which is designed to enable easier collaborations. It lets companies make the jump from local and networked hard drives to a cloud-based system where users can work with the same data. Desktop files can be synchronized to secure cloud storage, and everyone involved in a project can be on any platform and view and markup all common CAD formats. Teamcenter Share also has Augmented Reality (AR) capabilities. Users can see the model in context using their tablet or smartphone camera.
Taking it all the way out with IBM
It feels like the Siemens’ development of digital twin technology is happening in much the same way as Siemens expects its customers to develop digital twins for their products—it evolves as it goes. To this end, Siemens is adding on to its digital twin technology through an alliance with IBM’s Maximo group for SLM, service lifecycle management. Maximo is IBM’s Enterprise Asset Management (EAM) product family. Siemens and IBM’s work will combine tools from the Siemens Xcelerator portfolio and IBM Maximo to create tools at the edge to monitor systems, spot potential problems, and service assets.
Siemens and IBM say they are establishing a digital thread between product design, equipment manufacturers, and owner operators.
Talking about the alliance, Tony Hemmelgarn said it’s more fun to work with IBM as a partner than as a competitor, recognizing the shared interests the company has in asset management and ongoing service monitoring.
What do we think?
Siemens has lots more to talk about but the digital twin is at the heart of it and the company’s definition is straightforward. Every single company in the CAD business has signed on to the digital twin bandwagon, but Siemens is unusual for stepping up and stating it outright. The company also makes clear that its idea of the digital twin has to make room for data from a wide range of software programs, many of which are not Siemens products. We’re more used to seeing a fantasy description of digital twins that require users to live within a single software family. No one designing and building complex products like cars, washing machines, or industrial stamping machines can do that. But, that doesn’t stop Siemens from trying to build out as much of the process from conceptualization to service as it can. In the latest news from the company, we’re reading that the Mentor group has bought UltraSoc, a company from Cambridge, UK, that provides instrument and analytics solutions to add intelligent monitoring, cybersecurity, and functional safety capabilities into SoC cores. That technology will go into Siemens’ Xcelerator portfolio for SoC design in the Mentor business.
To read the report from last year’s press and analyst event, see: