The Jeff Koons studio employs almost 130 people including artists, sculptors, painters, modelers, and fabrication experts. The Koons retrospective at the Whitney reveals the artist’s attention to detail and exploration of new techniques. For example, Koons worked with 3D scan bureau Direct Dimensions and spent eight years creating a version of the Liberty Bell.
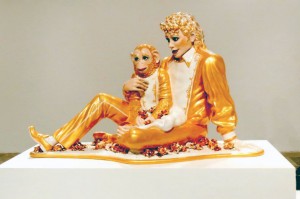
Jeff Koons has been a polarizing figure in the art world, still is in many quarters no doubt, but with the large retrospective exhibition of Koons’ work at the Whitney Museum in New York, it seems the art world is coming around. The exhibit is an important one for the Whitney, and represents the last major show before the museum shuts down to move to the Meat Packing District and a new building designed by Renzo Piano.
Given the scale of Koons’ work the show is the largest, and most difficult exhibition undertaken by the Whitney. In addition, Koons is the subject of positive stories in Vanity Fair, the New York Times, and Time. The stories recognize the almost insane commitment Koons has to his work and to his concept of art.
Koons has proven that he will go any lengths to get exactly the effect he wants for a piece. It’s an uncompromising concept that challenges the viewer’s thinking about “art,” (air quotes are discretionary). Among the pieces in the exhibition are his Play Doh piece, which was unveiled at the Whitney exhibit. On one hand, the Play Doh sculpture is just what Koons says it is: a representation of a pile of squashed, Play Doh globs, inspired by Koons’ son Ludwig at play. On the other hand, there is something decidedly scatological about the multi-colored pile, and if you had another hand, and you used it to touch the thing, you’d be surprised to find out it does not feel anything like clay. It is made out of cast aluminum. Koons spent 20 years trying to build the model. He had to wait for fabrication methods to catch up to his vision. According to an article in Art and Design, Koons was originally working in polyurethane, “but as I started putting more and more detail in the piece, I realized I needed to make it out of aluminum to get a more hyper-realistic surface.” In fact, Koons has helped push the evolution of aluminum fabrication by his demand for verisimilitude. One of his core ideas is to create pieces that exactly mimic common materials like plastic, Mylar balloons, plastic lawn chairs and children’s blow up models, but change the scale, the texture, or combine incongruous objects. Koons often recreates banal objects for us to think about in new contexts. Thus he has made a giant balloon dog. He’s made giant figurines in the style of Hummel that are even more appalling to encounter than the random piece found in the random grandmother’s over-stuffed apartment. He’s made Split Rocker, a giant, broken rocking horse head made out of flowers. And he’s made the famous gold and white statue called “Michael Jackson and Bubbles” that recreates a photo of the singer and his pet monkey in the garden of Jackson’s Neverland estate. The ceramic piece looks like some particularly awful statue created for a Russian Czar. Jackson and his monkey are porcelain white, and give us a lot to think about art, beauty, pathos, and Michael Jackson. Of this piece, Koons said in 1988 that if he could be any other person he would be Michael Jackson. “I wanted to create him in a very god-like icon manner. But I always liked the radicality of Michael Jackson; that he would do absolutely anything that was necessary to be able to communicate with people.”
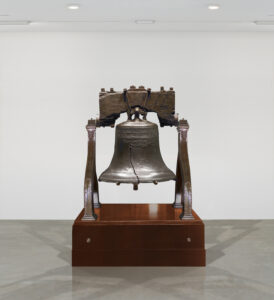
The Liberty Bell
Given Koons’ commitment to the process of creation and his exploration of fabrication techniques, then it’s natural he explore digital technologies including 3D scanning. Koons contacted Direct Dimensions, 3D scanning and printing consultants in Owings Mills, Maryland, as a result of work they did to help create the Normandy Bell, a perfected bell created for the 2004 60th Anniversary of the Normandy Invasion. In that case the project involved scanning the Liberty Bell in Philadelphia, and recreating the bell in 3D CAD (using Imageware). The goal was to recreate the bell as it was originally cast by Pass and Stowe in 1753, before the crack. The CAD model was sent to the Cornille-Harvard foundry in France to be recast.
Seeing that work, Koons contacted Direct Dimensions in 2006. The company’s founder and president Michael Raphael says they didn’t consider reusing scans created in 2004, instead, Direct Dimenions assembled the best 3D scanning capabilities they could put together 2006 and went back to Philadelphia to scan again. Raphael says 3D scanning, like 3D printing, computers, and CAD, all improve dramatically every year. “Given Koons’ purpose for this project – to recreate the Liberty Bell exactly,” said Raphael, “we knew we had to use the best available 3D scanning technologies. We used several – structured light, laser line scanners, and even developmental optical technologies not yet commercialized at that point.”
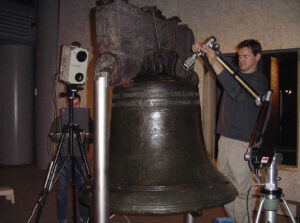
Structured light scanners project a regular pattern on the irregular surface of the object being scanned. The resulting distortions of the pattern can be measured to get the exact details of the surface but that was just the beginning. The Direct Dimensions team scanned the bell and the wooden head stock that holds it. After the bell was painstakingly scanned, says Raphael, “we used PolyWorks software (by Canadian company Innovmetric) to align, assemble, and mesh the 3D scan data for the main bell and headstock surfaces. We used Rapidform (now 3D Systems) to reverse model the mechanical components inside the bell into CAD geometry. Given the resolution and accuracy required for this project, it took many months to fully complete both styles of modeling in order to deliver a Koons Liberty Bell. The entire project took eight years to complete.
Ten Years later, and in time for the 70th anniversary of the invasion, Koons unveiled his Liberty Bell complete with signature crack for the Whitney. The two projects are almost exact opposites of one another. The 2004 Normandy Bell was recast, and the bell’s fabricators did their best to replicate the methods originally used to create a “perfect” bell. Koons also wanted to create a “perfect” Liberty Bell, identical in every way to the Liberty Bell that now resides in Philadelphia and so he had the bell milled in Germany by Arnold AG. (As with any Koons project, the irony runs deep in the work.) According to a detailed article in Vanity Fair, the Koons factory used painstaking methods to recreate the exact look of the bell. The bell was divided up into tiny grid spaces allowing artists to use stencils to perfectly and obsessively recreate the details of its surface.
One of the things about Koons’ work, in addition to the time and patience he puts into them, is the financial investment he makes in them, often employing dozens of artisans, engineers, and artists to create exactly what he envisions.
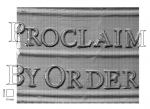
All this, is the kind of stuff that drives some people nuts about Koons’ art. Is it art it is it craft? Is it showmanship or chicanery? False questions of course; people might not like Koons’ art, but it is conceived and produced with layers of consciousness about process, intent, and the meanings in between. The Liberty Bell is a perfect example of this and it’s perfect that it is debuted at this important retrospective that makes such a strong case for the art of Jeff Koons.
Jeff Koons: A Retrospective
June 27-Oct. 9
The Whitney Museum of Modern Art
925 Madison Ave, New York 10021