Two third-year students successfully built only the third 3D printed aircraft to successfully fly.
By Fariss Samarrai
When University of Virginia (U.Va.) engineering students posted a YouTube video last spring of a plastic turbofan engine they had designed and built using 3D printing technology, they didn’t expect it to lead to anything except some page views.
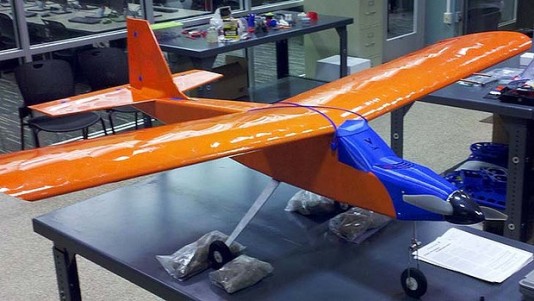
But executives at The MITRE Corporation, a federally funded research and development center in McLean, Virginia with an office near U.Va. in Charlottesville, saw the video and sent an announcement to the School of Engineering and Applied Science that they were looking for two summer interns to work on a new project involving 3D printing. They just didn’t say what the project was.
Only one student responded to the job announcement: Steven Easter, then a third-year mechanical engineering major. “I was curious about what they had to offer, but I didn’t call them until the day of the application deadline,” Easter said. He got a last-minute interview and brought with him his brother and lab partner, Jonathan Turman, also a third-year mechanical engineering major.
They got the job: to build over the summer an unmanned aerial vehicle, using 3D printing technology. In other words, a plastic plane, to be designed, fabricated, built and test-flown between May and August. A real-world engineering challenge, and part of a Department of the Army project to study the feasibility of using such planes.
It was a daunting project, producing a plane with a 6.5-foot wingspan, made from assembled printed parts. The brothers sometimes put in 80-hour workweeks, with many long nights in the lab. The two were mentored by their academic adviser, mechanical and aerospace engineering professor David Sheffler, a U.Va. Engineering School alumnus and 20-year veteran of the aerospace industry.
“It was sort of a seat-of-the-pants thing at first–wham, bang,” Easter said. “But we kept banging away and became more confident as we kept designing and printing out new parts.” Sheffler said he had confidence in them “the entire way.” A Stratasys Fortus 400mc was used to build the majority of the airplance. The team also used a Stratasys Dimension uPrint Plus for a few smaller parts.
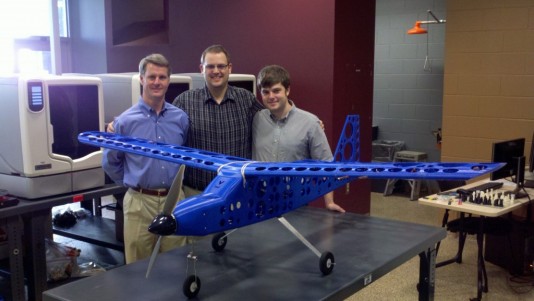
During the first test, the plane’s nose piece was damaged while the plane taxied around the field. “We dogged it,” Easter said. “But we printed a new nose.”
That ability to make and modify new parts is the beauty of 3D printing, said Sheffler, who works with students in the Engineering School’s Rapid Prototyping Lab. The lab includes seven 3D printers used as real-world teaching tools. “Rapid prototyping means rapid in small quantities,” Sheffler said. “It’s fluid, in that it allows students to evolve their parts and make changes as they go–design a piece, print it, make needed modifications to the design, and print a new piece. They can do this until they have exactly what they want.”
The technology also allows students to take on complex design projects that previously were impractical. “To make a plastic turbofan engine to scale five years ago would have taken two years, at a cost of about $250,000,” Sheffler said. “But with 3D printing we designed and built it in four months for about $2,000. This opens up an arena of teaching that was not available before. It allows us to train engineers for the real challenges they will face in industry.”
MITRE Corp. representatives and Army officials observed the fourth flight of Easter and Turman’s plane. They were impressed and asked the students to stay on through this academic year as part-time interns. Their task now is to build an improved plane–lighter, stronger, faster and more easily assembled. The project also is their fourth-year thesis.
“This has been a great opportunity for us,” Easter said, “to showcase engineering at U.Va. and the capabilities of the Rapid Prototyping Lab.”
Fariss Samarrai is a staff writer for the University of Virginia public relations bureau.