Cilllia automates design of individual hairs, bypassing manual methods in existing CAD tools.
By Amina Saeed
MIT Media Lab researchers have developed a method to print hair with an innovative software technique replacing traditional 3D CAD. The pixel-mapping printing technique allows users to model and print thousands of hair-like structures rapidly.
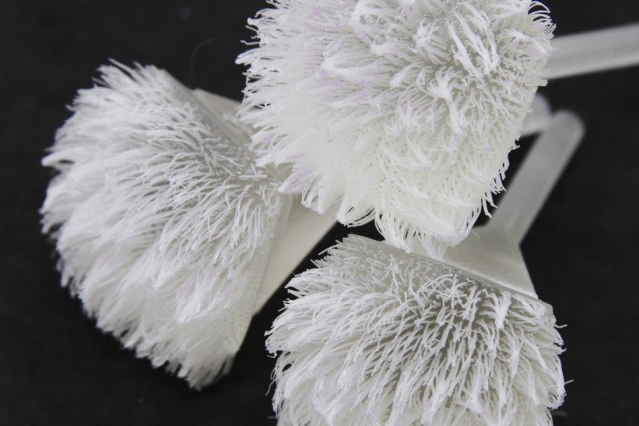
Previously, it took hours to design a set of thousands of hairs, but a new software tool called “Cilllia” allows the user to define angle, thickness, density, and height of thousands of hairs in just a few minutes. With the help of any conventional 3D printer, hair-like structures can be printed onto flat surfaces as well as curved ones using a resolution of 50 micrometers on screen—about the width of an average human hair.
The initial intention was to achieve useful tasks such as sensing, adhesion, and actuation and maybe create some toys. To determine the adhesiveness, the hair was printed as Velcro-like bristle pads. Depending on the angle of the bristles, the pads can stick to each other with varying forces. For sensing, the researchers printed a small furry rabbit figure, equipped with LED lights, which lit up when stroked.
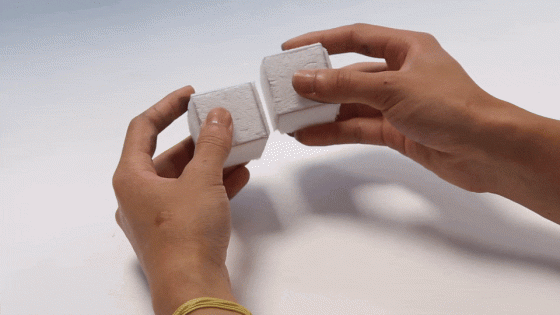
A small experiment was carried out to test the actuation of the 3D printed hair, whether it would move objects or not. The team came up with a weight-sorting table made from panels of printed hair with specified angles and heights. As a small vibration source shook the panels, the hairs were able to move coins across the table, sorting them based on the coins’ weight and the vibration frequency.
3D printed hair a software challenge
The real challenge arises during the software processes of making 3D hair. To 3D-print hair using existing software, designers need to model hair in CAD, drawing out each individual strand, then feed the drawing through a slicer program that represents each hair’s contour as a mesh of tiny triangles. The program would then create horizontal cross sections of the triangle mesh, and translate each cross section into pixels, or a bitmap, that a printer could then print out, layer by layer. All in all a very time consuming process.
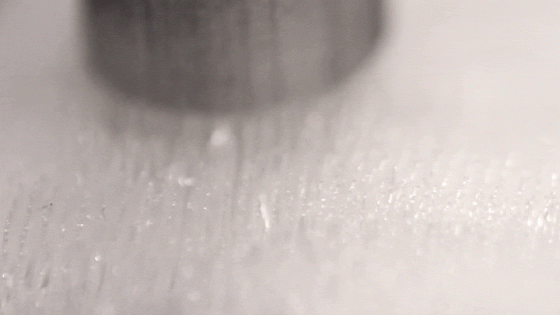
3D printed hair can be used for designing everyday interactive objects. In order to design hair, the researchers chose to do away with CAD modeling entirely. Instead, they built a new software platform to model first a single hair and then an array of hairs, and finally to print arrays on both flat and curved surfaces. Using these techniques, the team printed pads of Velcro-like bristles, and paintbrushes with varying textures and densities.
The tricky part comes when printing 3D hair onto a curved surface. In another experiment, the team first imported a CAD drawing of a curved surface, such as a small rabbit, then fed the model through a slicing program to generate a triangle mesh of the rabbit shape. After developing an algorithm to locate the center of each triangle’s base, they virtually drew a line out, perpendicular to the triangle’s base, to represent a single hair. Performing the same for every triangle in the mesh created a dense array of hairs running perpendicular to the rabbit’s curved surface. The researchers then used their color mapping techniques to quickly customize the rabbit hair’s thickness and stiffness.
Among other applications, 3D-printed hair may be used in interactive toys. To test this, the team inserted an LED light into the fuzzy printed rabbit, along with a small microphone that senses vibrations. With this setup, the bunny turns green when it is petted in the correct way, and red when it is not.