Acquisition by Autodesk has not slowed the pace of innovation.
The latest update to Delcam FeatureCAM includes more options for the Vortex high-efficiency area-clearance strategy, support for bar-fed mills, more efficient turning, and a variety of user-interface improvements.
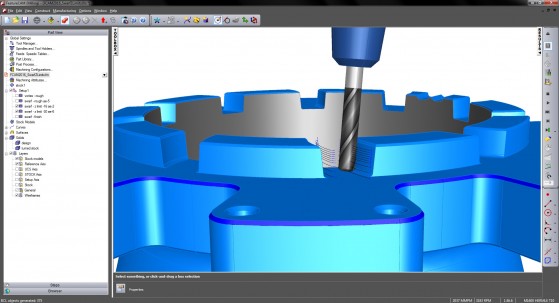
The 2016 release includes a number of enhancements to the Vortex area-clearance strategy. Delcam says Vortex gives the fastest safe metal removal from solid carbide tooling, especially for designs that give deeper cuts by using the full flute length as the cutting surface. Vortex clearance produces toolpaths with a controlled engagement angle, maintaining the optimum cutting conditions for the complete roughing cycle. Delcam says this in turn offers faster machining and longer tool life.
Also new is the ability to adjust and fine tune the non-cutting moves of 2.5D and 3D Vortex toolpaths, with options to retract the tool and/or to increase the feedrate. These options can be set individually, or can be combined to achieve an optimum toolpath, with a reduced cycle time.
Other roughing improvements include the ability to take into account any remaining stock on the model during holder collision checking, ensuring that Z-level roughing toolpaths are completely free of tool-holder collisions.
Milling of inside or outside groove features has been upgraded with a number of improvements. These include support for different types of roughing links, wind-fan approach and retract moves for finishing, better gouge checking for plunges and retracts, and tool radius and partline cutter compensation support.
Five-axis swarf machining has been made more flexible with a new option to control the upper and lower Z limits of a simultaneous five-axis swarf toolpath. This is useful if there are limitations on the tool length that can be used or if the stepdown needs to be varied for different segments of the toolpath.
For users of FeatureTURN, Delcam says the selection of turning tools has been simplified with the ability to use a single tool in multiple orientations. This new automatic tool orientation categorizes tooling into either outside-diameter or inside-diameter turning tools, shortening the time taken to program parts and reducing the number of different tools required in the tool crib.
FeatureCAM now allows the quick import and alignment of a variety of pre-defined vices and chucks into a machining project. Delcam says the result is increased productivity, not only due to the speed of programming but also because collision checking is provided automatically during simulation.
Used in combination with PowerSHAPE, FeatureCAM now allows machining files to be selected and nested automatically in a single block to optimise stock material usage.
Interface improvements include the ability to create additional setups quickly during Feature Recognition, via a new button in the Feature Wizard. This reduces the overall programming time significantly. In addition, items within the part view are now highlighted when the cursor hovers over them. At the same time, the items are also highlighted in the graphics screen, making it easier to find and select the desired items quickly.
Autodesk RealDWG has now been integrated into FeatureCAM, bringing with it increases in the speed of import of DWG files and support for DWG solid model import.
What do we think?
FeatureCAM was the world’s first feature-based programming software when it was launched in 1995. There were concerned in the CAM community of users that Delcam’s history of constant innovation and wide support of CAM hardware might change after it was acquired by Autodesk in 2013. But those concerns have been completely erased by Delcam’s continued pace of development and industry leadership. Holding it as a separate subsidiary has been a good strategy.