Time savings of between 40% and 70% have been achieved using the new technology.
Delcam introduces a new high-speed milling technology with the launch today of PowerMill 2014. The new Vortex high-efficiency area clearance strategy is a patent-pending process designed to gain the maximum benefit from solid carbide tooling.
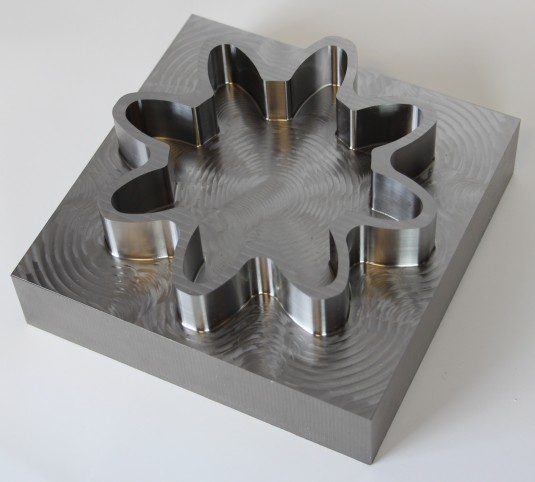
Like other Delcam roughing strategies, Vortex toolpaths are calculated to give more efficient machining by following the shape of the part and by keeping air moves to a minimum. Delcam the Vortex technology is particularly useful in designs where deeper cuts can be created by using the full flute length as the cutting surface. It can be used for two- and three-axis roughing, three-plus-two-axis area clearance and for rest machining based on stock models or reference toolpaths. Delcam says the benefits of the Vortex strategy will vary depending on a number of factors, including the material and shape being cut, and the machine tool and cutting tools being used. A series of trials run by Delcam on different machine tools within its Advanced Manufacturing Facility has shown a time saving of at least 40% is not untypical. The greatest reduction in cutting time was accomplished using cutting tool steel on a Huron machine with SGS Z-Carb MD cutters; Delcam says the cycle time for the sample part was reduced from 121 minutes to 34 minutes, a reduction of 71%. Other examples included a reduction of 67% when cutting a number of pockets in a stainless steel part, a 63% time saving on a titanium part and a 58% saving when cutting an aluminium component. Most high-speed roughing techniques aim to maintain a constant theoretical metal-removal rate; the Vortex strategy produces toolpaths with a controlled engagement angle for the complete operation. Delcam says this approach maintains the optimum cutting conditions for the entire toolpath that would normally be possible only for the straight-line moves. As a result, cutting time is reduced and cutting happens at a more consistent volume-removal rate and feed rate, protecting the machine. “Anyone using the Vortex strategy will be able to hear the difference immediately,” claims Mark Forth, product manager for Delcam’s Advanced Manufacturing Solutions. “Conventional roughing produces a sound of varying pitch, which indicates that the optimum cutting conditions are not being used and could even be a sign of tool overload or chatter. In contrast, Vortex roughing gives a constant pitch, showing that the tool is operating under consistent conditions. Users will also be able to see the difference in the regular size and thickness of the chips produced, providing further evidence of the consistency of the cut.”