Intriguing but pricey. Steve Wolfe takes a close look at the most highly anticipated new MCAD product in years.
By L. Stephen Wolfe, P.E.
[Editor’s Note: Larger versions of the images in this article are available on the GraphicSpeak Facebook page.]
As reported on January 28, the SolidWorks division of Dassault Systèmes announced the first release of software dubbed Mechanical Conceptual, based on what DS now calls the 3D Experience Platform. Intended for sale through the SolidWorks dealer channel, it’s the first of a new family of SolidWorks products.
As noted in the previous GraphicSpeak article on the new software, first customer deliveries are planned for April 2014. The asking price is $2,988 annually for a named-user license.
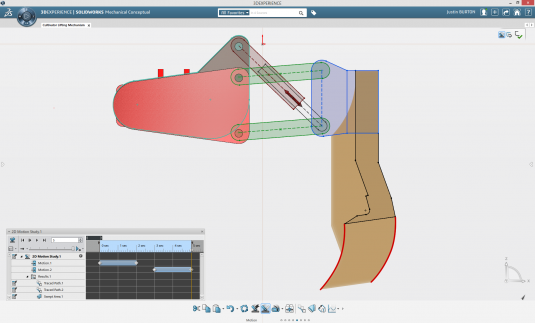
Only one person can access a named-user license, although SolidWorks says the license may be transferred to another person after 30 days. In contrast, for a modest extra fee, a license for the original SolidWorks software package may be shared by several employees on a network as long as only one person at a time is using it.
Given the relatively high cost and functional limits of SolidWorks Mechanical Conceptual, it’s worth exploring the business case for using it. What does it do that can’t be done with the existing SolidWorks software? How could it make engineers and their employers more efficient? What other economic benefits might accrue to users of this software?
Unique capabilities
As its name implies, Mechanical Conceptual is currently intended for preliminary design of machinery. Its forte is machinery with mechanisms such as linkages, cams, joints, and other moving parts. It does not currently have tools for designing aerodynamic or hydrodynamic surfaces, nor free-form curvature-continuous surfaces of the sort favored by industrial designers. It has no specific functions for sheet-metal design or electrical wiring. It can’t produce molds or dies.
Impromptu demonstrations at the 2014 SolidWorks World conference combined with testimony from some of so-called “lighthouse customers” who used the software prior to the announcement indicate that for designing mechanisms, Mechanical Conceptual is significantly faster and easier to use than SolidWorks V1 (as Dassault Systèmes executives have started calling the original SolidWorks software).
Foremost among the new capabilities is the improved sketcher in Mechanical Conceptual. Although not as intuitive as pencil and paper, the sketch tools are much more powerful. Closed profiles are automatically turned into blocks that can be linked together to form mechanisms. Constraints such as tangent curves and right angles have been made simpler to apply. Constraints between blocks are not just geometric, but they also constrain motion of the blocks, so linkages can be modeled quickly. The software automatically displays swept areas of a mechanism, so interference with other parts of the machine can be discovered quickly.
Once sketches have been refined to a designer’s satisfaction, profiles can be extruded or revolved to produce solid bodies. These objects retain the kinematic relationships defined in the sketch. Cuts, bosses, and edge rounds can be added to the solid objects to produce basic machine elements.
Unlike parts of assemblies in SolidWorks CAD, Mechanical Conceptual parts need not be saved as separate files when they are created. It is also possible to import parts or assemblies from SolidWorks CAD and use them in Mechanical Conceptual models.
Mechanical Conceptual has powerful capabilities for editing solids. Designers can directly pull or push on faces or add sketched features to solid objects.
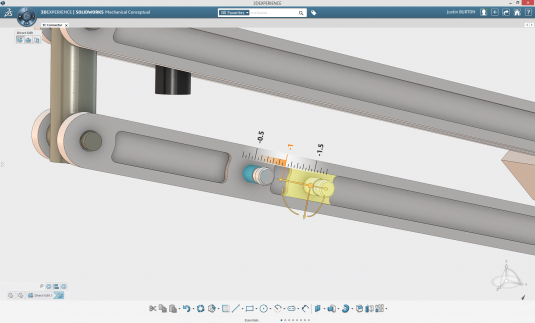
Combining direct editing of CAD solid models with features in a history tree has vexed CAD software developers for years. Solutions have ranged from blowing away the entire history to adding direct-edits to the end of the history tree.
SolidWorks has devised a unique approach to the problem. When designers select a face to be pushed or pulled, the corresponding feature to which it belongs highlights and the software asks if the designer wants to convert it to a direct-edit feature. If the designer says yes, the feature is converted and the face can be dragged. The direct feature retains its place in the feature history along with the others.
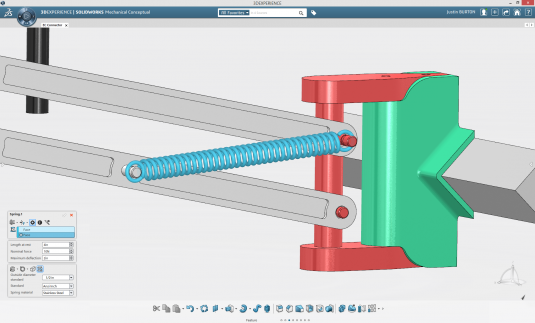
In the future, Dassault Systèmes plans to offer finite-element-analysis software for predicting stresses and deflections in Mechanical Conceptual. But these design aids, when they are ready, will cost extra.
Collaboration
The second major benefit of Mechanical Conceptual is the ability to share models in real time with other engineers, workers and managers in other departments (such as sales or manufacturing), suppliers, and potential or current customers. With SolidWorks CAD, sharing models requires zipping up a set of files from an assembly or making an eDrawings (or other derivative format) file. The files are then sent via e-mail or put on an FTP site or in a Dropbox folder to be downloaded by the recipient. SolidWorks users also can share their models by hosting a session on WebEx or a similar screen-sharing service.
Besides requiring extra steps, sharing files has other disadvantages. Once a file is sent, it can’t easily be recalled. (There are so-called digital rights management applications that can take away the ability to view an encrypted file, but I’ve never heard of any CAD user who tried them.) And with files outside the control of a PDM system, there is always the possibility that the customer or co-worker will look at the wrong version.
Mechanical Conceptual introduces a new way of sharing data that’s integral to the 3D Experience Platform. Called the 3D Dashboard, it functions like the Windows Explorer for SolidWorks or any other desktop application. All models are saved to the dashboard in a so-called workspace that can be shared with co-workers or customers. The dashboard is accessible by a Web browser. Clients who don’t have Mechanical Conceptual can simply log in to view models.
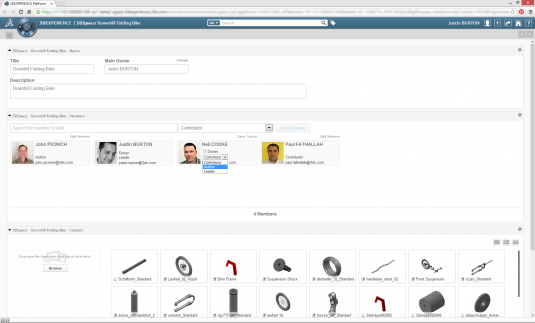
Designers can control who has access to models they created and what they can do with them. Other people may be allowed to view models, add comments, or make changes (if they have the Mechanical Conceptual software). Permissions to view or modify models can be removed. So, for example, a supplier whose bid has been rejected may be denied access to a model for which he has made a quotation.
The collaborative dashboard and the models made in Mechanical Conceptual are not stored on a designers workstation but in a “cloud service” operated by Dassault Systèmes. Models are not stored as collections of Windows files but in a database similar in concept to Catia V6. (See “Is Catia V6 over the hump?” for details.) This architecture may explain why Mechanical Conceptual cannot be operated without an Internet connection. SolidWorks representatives said future versions of Mechanical Conceptual may enable models to be stored on local hard drives so that designers can work in places where the Internet is unavailable.
Dassault Systèmes employees gave conflicting reports about whether the CAD giant had built its own data centers to house the cloud servers or was instead renting machines from “Amazon and other service providers.” But as with other cloud services, customers do not know and need not care where their data resides. It is accessible anywhere that a customer can log in.
Unlike applications such as Google Drive or the Lagoa rendering service that require only a basic browser, Mechanical Conceptual requires users to download and install a relatively large program that runs on their desktop computers. Upon release, the Mechanical Conceptual software is supposed to download and install automatically from a Web browser, and once it is installed, it can be used by anyone with a log-in name and password. One Lighthouse customer said this automatic installation was not available during the trial period.
At SolidWorks World, the company also announced that some form of the 3D Experience Dashboard also would be available with SolidWorks 2015, planned for delivery in the fall of 2014. Although this service is likely to be welcomed by many SolidWorks customers, its availability may dispel some of the incentive to buy Mechanical Conceptual.
Importing into SolidWorks
Assuring designers that a model will work is about as far as Mechanical Conceptual can take them. It does not make drawings or allow models to be annotated with tolerances (also called “product manufacturing information” (PMI)). It cannot bend or unfold sheet metal, route wires and cables, design mold inserts, or simulate mold filling and cooling. Mechanical Conceptual has no interface to software for programming numerically controlled tools or inspection machines. And it lacks tools for adding details such as decals or engraving. To finish the design and manufacturing process, Mechanical Conceptual models must be imported into SolidWorks.
The importing of Mechanical Conceptual models into SolidWorks should be a relatively easy process, with some limitations. Prior to importing, Mechanical Conceptual users can individually name each body in the design. Each named part will then be imported into the SolidWorks CAD software as a 3D part file in an assembly model.
SolidWorks CAD employs Siemens’s Parasolid kernel for solid model geometry, while all 3D Experience Platform products employ the CGM kernel developed by Dassault Systèmes for the Catia CAD software. According to Gian Paolo Bassi, SolidWorks vice president of R&D, both kernels employ non-uniform rational b-spline surfaces (NURBS). So the shapes of models can be imported and exported with high fidelity. What is lost in translation are dimension-driven features defined in SolidWorks Feature Manager or the feature history tree of Mechanical Conceptual.
What customers think
Most customers and dealers we spoke with at SolidWorks World said they didn’t know enough about Mechanical Conceptual to form an opinion. SolidWorks put six of its Lighthouse customers, who have used the software since midsummer 2013, on stage to give their impressions of the product.
Three of the customers, Mike Buchli of Karl W. Schmidt, Thorsten Rettich of J. G. Weisser Söhne, and Bernd Knab of PolyRack said they found Mechanical Conceptual to be most useful for sharing designs with customers at the pre-sales stage. Buchli volunteered that his company uploaded a 20,000 part SolidWorks assembly over a 3-megabit Internet connection and that it worked pretty well. The three others, William MacLeod of Kennedy Integrated Hygiene, Adam Whittingham of OLEO International, and Phil Sluder of Tri-Axial Design and Analysis, said they found Mechanical Conceptual to be faster than the original SolidWorks for developing multiple design concepts for early evaluation.
The fog is lifting
SolidWorks Mechanical Conceptual is being billed as a “concept modeler.” So was Pro/Engineer when it was rolled out in 1987. But PTC executives intended from the beginning to make it a complete CAD/CAM system with a full suite of specialty applications, and they succeeded. Dassault Systèmes executives plan to supersede the existing SolidWorks CAD software with design-and-simulation aids based on the 3D Experience Platform (formerly known as the Catia V6 Application Architecture).
The transition, if it is successful, is likely to take 10 to 15 years, given the enormous size of the SolidWorks customer community. The next step in the process will be the release of SolidWorks Industrial Conceptual early in 2015. This software is intended for industrial designers who make highly styled products with free-form or aerodynamic shapes. It will include some of Dassault Systèmes’ best surfacing software developed for the Catia CAD software and used by major automotive and aircraft OEMs.
Just how SolidWorks will knit these various offerings into a complete design system remains murky at this time. So Dassault Systèmes executives are not about to announce the end of life of the original SolidWorks software. Based on the impressive improvements previewed for SolidWorks 2015, the company is continuing to aggressively improve its flagship product.
What do we think?
SolidWorks Mechanical Conceptual embodies some intriguing technology, but at the current asking price it will appeal to only a narrow segment of SolidWorks customers. Large firms may rent a few seats for sales support or conceptual design, but the software doesn’t do enough to justify a nearly $3,000 per year price tag.
If Dassault Systèmes wants SolidWorks customers to sample the 3D Experience Platform in large numbers, it must offer much more attractive pricing. Speaking before a SolidWorks World general session, one customer suggested including Mechanical Conceptual free with a paid annual subscription.
Autodesk, in keeping with its low-priced heritage, is asking just $300 per year for its web-based Fusion 360 CAD software. And Autodesk offers a generous free-trial period for Fusion 360 as well.
One advantage of a high initial price is that it enables Dassault Systèmes to roll out Mechanical Conceptual slowly. If hundreds of thousands of SolidWorks customers logged in to Mechanical Conceptual at once, it could blow out the lights at several large data centers.
L. Stephen Wolfe P.E. is the 2004 award winner of the CAD Society Lifetime Achievement Award, a consulting engineer registered in the state of California, and one of the world’s best-known reviewers of engineering software. Wolfe holds a master’s degree in Mechanical Engineering from MIT, and a BSME from Northwestern University. He also attended the University of Chicago graduate school of business. He is a consulting analyst for Jon Peddie Research.