Increasing the communication between engineering and the factory floor has developed significantly, but still has a long way to go. From the April 2007 edition of Engineering Automation Report, acquired in 2010 by Jon Peddie Research.
By Nick Ballard and Peter Thorne
Cambashi Ltd.
Engineering Automation Report, April 2007—Siemens’ intention to purchase UGS has provoked debate about the future of manufacturing industries, the relationship between PLM and automation, and the strategies that manufacturing companies will adopt. This has created a lot of opportunity for “what if” speculation. We want to take a closer look at a few of these “what if” themes.
In recent years, the communication between PLM and plant operations has developed significantly. What was a one-way delivery of drawings, test specifications, recipes, programs for production equipment and so on has changed to a two-way exchange, with plant operations feeding back information such as change requests, as-built history, test results and more in a structured way.
What if new levels of agility of automated production systems are possible? PLM users have often demonstrated improvements in their capability to obtain agile response from their production assets. Perhaps there are automation options that would amplify these results. Agility quickly turns into cost savings when market demand is for constantly changing products, and when there is unpredictable fluctuation in demand. In recent years, outsourcing has been a leading cost-saving production strategy. Could cost savings based on agility make investment in PLM and automation a real alternative to outsourcing in more situations?
Today’s production processes must deliver not only the tangible product, but also a range of intangible information that is a bi-product of the manufacturing activity. For example, tracking and traceability information, as-made batch history, customer and supplier triggers for supply chain management, test results for compliance monitoring and so on must all be available. This information has to be integrated with the information from traditional sources such as marketing material and service information, and delivered alongside the product to people or systems in partner and customer organizations.
The infrastructure needed to gather, manage and deliver product information related to each tangible product is certainly non-trivial, especially in an agile environment. Perhaps the value of a factory-of-the-future will depend on its capability to receive, process and deliver product-related information just as much as its capability to receive, process and deliver tangible goods. The interaction between PLM and automation systems is a critical piece in the IT puzzle that delivers this capability.
The next “what if” is to do with the future of the information highway between design, manufacturing, supply chain and in-life service.
Right now, this highway is a little like a distribution service. Product and production information can be packaged and moved around quite effectively. But in many cases, the timely, complete transmission of information, and the communication of the right context for the information, depends on the ingenuity of people at both ends of the link. Sometimes, obtaining status reports of what information, and what versions are being used at which stage of the process is automatic and easy. But in many environments, it takes the online equivalent of a walk around the warehouse and all the receiving bays to find out what information is where!
Toward a shared database
What if, in place of a distribution service, this particular information highway developed the speed and reliability of a shared database? Information from the production side would be available in database records containing views of real time sensor information, and other records containing aggregated, analyzed information from factories around the world—not for a few special data items, as now, but for everything. The vision is tempting. For example, imagine a designer opening an on-screen window containing automatically-generated cost and delivery-date feedback based on the current set of parts and features in a design. Today, this information is usually an estimate, generated from locally held software models and various rules of thumb. But perhaps the calculation could be based on live data being generated by and collected from all the remote locations capable of manufacturing the part.
This is one example of replacement of information system elements that model the real situation with an alternative source, namely, readings taken from physical sensors that measure and report the real situation. This possibility opens up some critical choices in information system architecture. Nowhere is this more obvious than in supply chain and inventory management. Which report would you prefer—the one generated by reading the locations and quantities of materials directly from sensors (in warehouses, trucks and factories), or the one generated by the software models maintained by ERP systems? If you want a current status report, then naturally, the sensor based information will be more valuable. But if you are trying to simulate what will happen if you force through a priority order, then the software models become vital. To respond to a supply chain incident successfully, sensor information must report the incident and the real-time status, but software models are needed to determine the optimum response, so the real need is for integrated access to both sensor and model information.
The question of where the intelligence really lies has long been an issue for factory and plant automation designers. What is the optimum way of distributing functions between a sensor, a local controller, a manufacturing execution system and a production planning system? And how is the information held by those systems communicated between them? How can the rest of the enterprise be connected? ISA-95 (known as S95 prior to 2003) is a set of standards for integration of enterprise systems to plant operations. Together with a business-to-manufacturing mark-up language (B2MML), ISA-95 is currently in use in a range of projects—at Eli Lilly, for instance. Use of a standard together with a mark-up language is intended as a flexible way to structure and simplify the transfer of information between the various manufacturing and enterprise levels. The target is integration of real-time manufacturing data into other applications, like enterprise resource planning and quality management systems.
An example from the enterprise side is SAP’s “xApp Manufacturing Integration and Intelligence” module (XMII), which provides B2MML as a predefined schema for data mapping and communication. An example from the plant floor is Siemens’ “Cross Industry Library” (CIL) software components, which are used to connect SIMATIC automation solutions to B2MML compliant (and other) modules. Part of the ISA 95 and B2MML specifications cover data structures for “product Definition.” By PLM standards, the scope of the Product Definition is quite limited, understandably focusing on the aspects of product definition required for production management.
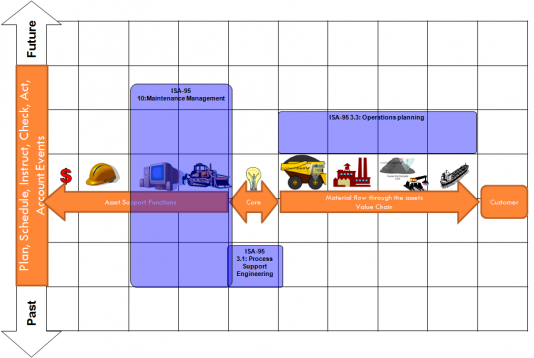
More complete product definitions
But what if automation systems could access a more complete product definition—not just production management information, but something closer to a PLM product definition? Would this extend automation possibilities? For example, perhaps there are better ways of closing the loop between design and production—the production system may be able to execute deeper comparisons between the original requirement and as-made information, and make more fundamental adjustments to optimize production. Or perhaps more automation of in-line testing becomes possible, because the test controller can calculate its own test sequences.
Of course, there are still barriers between enterprise IT departments and those that manage industrial control and automation systems. These groups are “both on the same side” but tend to view each other with skepticism when it comes to understanding each others? specific IT requirements. For example, a bug on the enterprise side may delay a report, whereas the same on the factory side can break machine tools, bring down a production line, or cause a safety incident in a chemical process.
What if these barriers disappear? Perhaps, together with new industry structures on the vendor side, this would create the environment for new insights into the relationships between the real world of tangible goods and the virtual world of PLM. As always with manufacturing, these visions of new sources of competitive advantage need to be blended with a healthy dose of pragmatic realism. But if no one dares to be first, then nothing changes. Go on, have a go!
Nick Ballard and Peter Thorne are staff analysts with Cambashi Ltd., Cambridge, UK.