Swift Engineering studies wake patterns to find new competitive approaches.
The race does not always go to the swift, especially when it’s Formula racing, where the wake of a race car can be turbulent enough to prevent others from passing it, no matter how fast they’re going.
“That can make it pretty boring to watch, as well,” said John Winkler, Ph.D. and Chief Aerodynamicist at Swift Engineering Inc.“Less passing means fewer contests for the lead. Cars line up behind one another and just go around the track until they near the end. Many believe this has taken away from the overall excitement of the sport.”
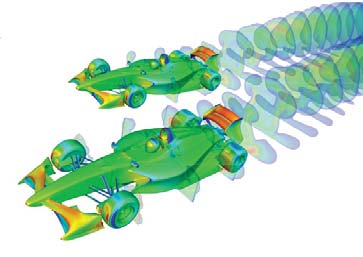
Now it’s Swift that’s going to the race, so to speak, with some innovative new designs to help make it more exciting to watch. This is not the first time the company has dived into Formula racing. Swift Engineering’s design and composite manufacturing innovations have yielded championship winning race cars for nearly thirty years, from its early Formula Ford design in 1983 to the present Formula Nippon carbon fiber race car, which is capable of speeds approaching 200 MPH and 4 G cornering.
Busting a few mushrooms
“It began when we started talking about what we could contribute, as designers, that could make racing more interesting to watch,” said Winkler. “One idea was to increase the number of times the lead can change by making it easier for cars to pass each other. The answer to that was to do a little mushroom-busting.”
Winkler is referring to the shape of the wake left behind by the rear wing of the race car, which looks like a mushroom when visualized and viewed from the rear. By reshaping the wake and moving it up and away from the racetrack surface, Winkler and his team are trying to remove or reduce this very turbulent obstacle to cars attempting to pass, using Tecplot Chorus to visualize the physics involved.
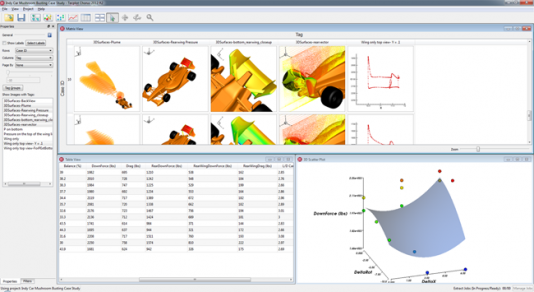
Process overview
Working with Swift’s Chief Scientist Mark Page and Aerodynamicist Andy Luo, Winkler began by developing a simplified perturbation study on the rear wing of the Swift 017.n wing to get a better understanding of how changes in the wing’s position and rotation affect aerodynamic performance as well as the shape of the wake downstream.
“Although we were examining ways of changing the shape of the wake downstream, it was equally important to make sure we did not sacrifice performance,” said Winkler. “Increasing the enjoyment and excitement of watching a race is one thing, but it would defeat the purpose if the car is slower, can’t corner as well, or is generally less responsive.”
They then used the qualitative flow visualization results to explain trends in the quantitative aerodynamic parameters such as downforce and drag. Finally, they used the knowledge gained to tailor a design that could promote passing without sacrificing performance.
Grid and solver
Winkler and Luo created a hybrid mesh with a completely structured far-field and an unstructured grid around the car. Using the Tecplot Metacomp CFD++ flow solver, with the car running at 150 miles per hour in a standard atmosphere at 59 degrees F, the initial run took almost nine hours on an in-house HPC cluster. The team then interpolated the original run as the initial condition for the subsequent runs, cutting the computing time to about 3.5 hours per run.
The results were imported into Tecplot Chorus for further analysis, where Luo and Winkler created surrogate plots of the overall vehicle downforce and rear wing downforce. The plots revealed some peculiar and unexpected results, especially in the cases with rotation.
“With only small changes in the wing’s orientation and position, we saw significant changes in the performance results,” said Luo. “That was one thing we were scratching our heads over. If the wings were moving only slightly, how was there such a big difference in the numbers?”
Luo and Winkler then used Tecplot Chorus to look at and compare surface pressures on top of and beneath the wing.
“As we went into the qualitative assessment of different runs, the downforce numbers were telling us that something was different, something drastic was happening,” said Luo. “But we didn’t know if it was valid. It was only by stepping through these comparisons that we could confirm what we saw was real, not an error.”
The final step was to generate a series of symmetry plane cuts showing a cross section of the wing and the flow around it. This helped explain the physics and confirmed that the downforce numbers were correct. One of the most interesting findings the process yielded was that optimal performance also generated the highest, least obstructive wake.
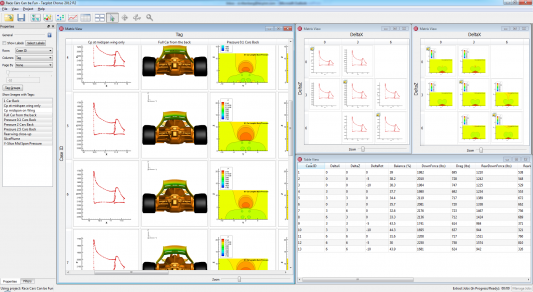
The current study was only a preliminary investigation to help the engineers better understand the sensitivity of the rear downforce and wake shape in relation to wing position and incidence. It involved a small number of perturbations and a small number of design variables. The next steps will be to expand the study to include more design variables, perform a DOE to isolate design variables with high sensitivities, and drive CFD++ through an outer optimization routine.
Winkler and Luo both agree that Tecplot Chorus facilitated the comparison of multiple visualized flowfields in an efficient manner. The results from these comparisons helped to explain the peculiar downforce and drag trends, while the cut-planes in the wake downstream highlighted the wake movement as a function of the perturbed parameters.
“From a designer’s standpoint, it is important to understand why a certain concept or design is better than another,” said Winkler. “Inspecting the flowfield is a key component of the aerodynamic design process, because it allows the designer to not only validate the solution but also to gain a better understanding as to how certain design variables affect the flowfield.”
While this type of comparison may have been done in another visualization tool using scripts, Tecplot Chorus made it easy to organize, catalog, and visualize all of these solutions.
“One of the best things about Tecplot Chorus is that it lets me spend more time working the problem and less time troubleshooting and writing scripts,” added Luo. “What once took me four or five hours, now takes me only five or ten minutes. And I would much rather invest my time in solving engineering problems for my customers than waste it on tedious tasks like writing and managing scripts.”