Autodesk, Citi, and UC’s Terner Center team up to find new solutions to a very old problem.
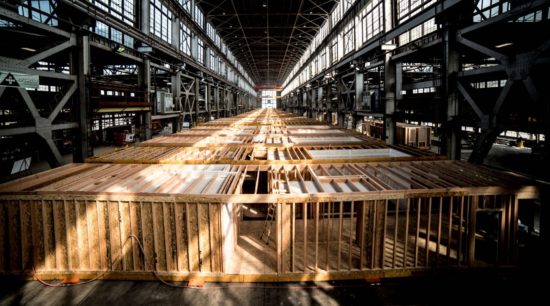
The Bay Area is grappling with a crippling housing shortage that has gotten more acute as a result of several ruinous fire seasons, rising home prices, and reduced building due to permitting and neighborhood restrictions. Working-class neighborhoods are disappearing from San Francisco and putting pressure on nearby communities including Oakland, Berkeley, Vallejo, and Richmond.
Factory OS, based on Mare Island, is located on the edge of the Bay Area’s shifting economics and the company is trying to change the equation so that more affordable housing can help preserve the character of communities. The company was originally founded to improve the efficiency of large construction projects. They build apartments as modular units in factories using an assembly line approach, and then the blocks of apartments can be taken to the construction site and slotted into the building frame.
The company believes it can address some of the problems Northern California is experiencing by modernizing construction and making it more efficient—efficient, like manufacturing.
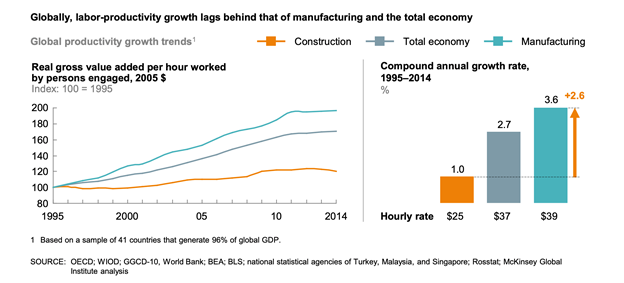
Factory OS is using pre-fab approaches to enable multifamily homes to be built more affordably and sustainably. Most recently, Bay Area local news has reported that Factory OS has been able to do the principle construction on a 110 unit multi-family project in West Oakland in 10 days. The project was designed by David Baker architects and built by Holliday Development, which is a construction company owned by Factory OS CEO Rick Holliday. The project, called The Union, has been able to put the building up with comparatively low impact on the neighborhood because the units were built a few miles up north in Vallejo at a Factory OS site. The major work of this product has been done in the years leading up to the actual construction on the site.
Autodesk is buying into the Factory OS’ vision and has made an investment in the company along with Citi. The investments are made to try and improve the housing crisis in the San Francisco Bay Area. The investments are also evidence of Autodesk’s focus on the construction industry as a major opportunity for the company.
Autodesk, Citi, and Factory OS are hoping to further the development of new practices for the construction industry through the Factory Floor Learning Center, which is being led by the Terner Center for Housing Innovation, a joint product of the University of California, Berkley, and the Haas School of Business.
They’re also building a new factory space called the Rapid Response Factory, which will work on the development of new machining techniques to meet the demand of quick turnaround housing needed after natural disasters and emergencies.
Citi’s Spread Products Investment Technologies (SPRINT) initiative was formed in 2018 to help finance affordable housing and community development projects.
New tools are needed and the challenges are becoming increasingly evident. There is evidence of our decaying infrastructure all around us, the housing shortages being experienced in San Francisco are being repeated worldwide and not just in large rich cities like New York, London, and Tokyo, but also in cities being hit by rapid growth as people move from the country to the cities in Asia, or in postindustrial cities like Detroit and Philadelphia which continue to fall behind if they can’t create housing for young workers.
In March 2019 at an Emtech Digital conference in San Francisco, Andrew Anagnost talked about the ways in which he sees design, development, and production changing through the use of AI and machine learning. He told the audience that Autodesk has understood that the process of creating models is not a value-added proposition and that, in fact, the tools are getting in the way of production. Add to that the process of construction, which has not changed dramatically for a hundred years. For the most part, it still depends on poorly paid workers doing dangerous jobs onsite and often in difficult conditions. There is also a labor shortage that is becoming more obvious as anti-immigration efforts reduce the labor pool.
At Emtech, Andrew Anagnost told host David Rotman to think about the construction site as an open-air factory and he notes that the construction industry has an unacceptably high rate of onsite accidents and death. Autodesk believes the system needs to be turned around by putting more of the effort of building into pre-fabrication in controlled environments where the work can be safer, more pleasant, and better paid.
He said that Autodesk is gathering mountains of information from construction sites around the world using drones, inspection reports, RFID information, scans, all available tools to build AI tools that can help with the design process. He says, it might not happen soon, but we are headed inexorably to a time when the tools companies like Autodesk will enable people to enter in the requirements and constraints for a project and geometry can be automatically generated freeing up designers from laboriously building models and instead make design decisions based on generated models. This is a process Autodesk sees transforming manufacture as well as AEC.
As it happens, California has become an unwilling incubator for new ideas and processes around addressing the housing crisis. After the fires of 2017 and 2018, an already terrible housing situation has become a crisis with thousands of people being displaced and projects are being held up by zoning restrictions, slow permitting processes, and expensive land acquisition.
Anagnost says that even incremental improvements in construction have the power to unlock financial benefits. He sees projects like those Factory OS is taking on as having the potential to increase pressure on local bureaucracies. If the building process becomes more efficient, then that helps highlight the need for faster permitting and land acquisition. Research by the Terner Center has revealed that local government fees on housing in California are three times the national average and the fees are not even clearly detailed and outlined upfront causing many needed projects to fail before they even get off the ground.
It may be too early to hope, but the falling dominoes of California’s disasters are driving new legislation to force cities and counties to become more transparent about fees and regulations. Meanwhile, improved building techniques have the potential to shorten the time to market for new housing. Waste and inefficiency in the construction industry is well understood, but improvement has been slow to evolve but one truth plays out over and over again. As industries become digitized, they become more efficient and new economic opportunities are unlocked. The time is right for construction and what’s happening in California is just one indicator.