The PTC pivot into an Internet of Things business is part of a larger redefinition of manufacturing.
Today at the PTC LiveWorx 2016 conference, CEO James Heppelmann ended his presentation by introducing a new logo to represent the company. As shown here, the new logo combines the company name (they stopped being “Parametrics Technology Corporation” years ago) with a stylized “d” and “p”. The logo symbolize the merging of digital and physical.
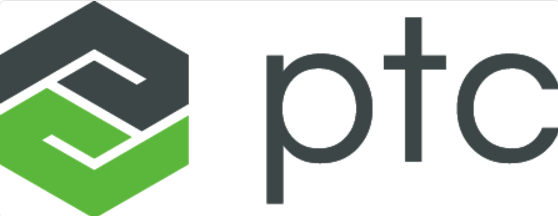
What do we think?
Why do we care about a new logo? Because more than most corporate rebranding actions, this one truly symbolizes the rebirth of a company into a new and fascinating place.
PTC stormed the CAD market in the late 1980s because it brought together two concepts: computer-based engineering for product development and 3D graphics. For a generation its software has been working at the crossroads of digital technology and physical manufacturing. A few years ago new CEO James Heppelmann bet the farm that PTC’s future was to once again define the crossroads of the digital and the physical. “We are uniquely positioned for the next wave,” Heppelmann told the crowd of 4,000—an attendance record for a PTC event. Recent acquisitions have created a portfolio that allows manufacturers to incorporate not only Internet of Things (IoT) data connectivity but also artificial intelligence, virtual reality, and augmented reality into a suite of products, platform services, and applications that redefine manufacturing, product servicing, operations and even marketing. Betting the farm seems to have paid off.
An on-stage demonstration at Liveworx 2016 by PTC customer Flowserve proved the truth behind the rebranding. Working with PTC’s IoT products during development, they created a technology that combines technologies from PTC, Ansys, HP Enterprise, and National Instruments to turn flow monitoring into a digital process, including real-time simulation of flow issues in a device. The ramifications are staggering: one shutdown of an oil refinery to solve a flow issue is a $1 million per hour problem. Yet 50% of all flow sensor anomaly reports wind up being of no consequence, and it often takes three trips to the site of the problem to resolve an issue. “The artificial intelligence in ThingWorx Analytics can tell you if the data is important and actionable or normal,” says Eric van Gemeren, VP of R&D at Flowserve. “Context is crucial.” van Gemeren estimates US manufacturers could generate savings of $20 billion per year by maximizing asset performance with such technology.