The Wizard, part of its new iMachining module, is now available in SolidCAM 2011. The company is a Gold-certified SolidWorks developer.
SolidCAM claims its new iMachining milling software offers a significant improvement over existing computer-aided maching software, due to a new knowledge-based Technology Wizard. The module is part of SolidCAM 2011, now available as an add-on to SolidWorks.
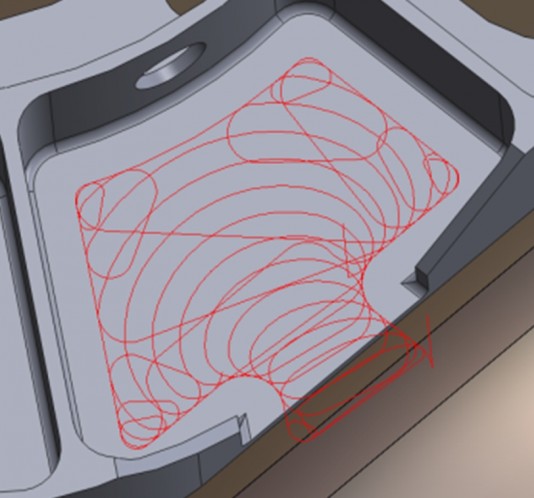
Based in Brno, Czech Republic, SolidCAM has been developing CAM tools for 23 years and was an early third-party application for SolidWorks. The company claims its new iMachining technology optimizes tool engagement and cutting feed through the entire tool path, reducing cutting times by up to 70% by allowing deeper and more efficient cutting.
The Technology Wizard takes into consideration the machine being used, the material being cut, and the entire geometry and material of the cutting tool. It then calculates the most efficient tool load, one that makes every effort to machine with the full length of the cutter, instead of just the tip as is more common in CAM applications.
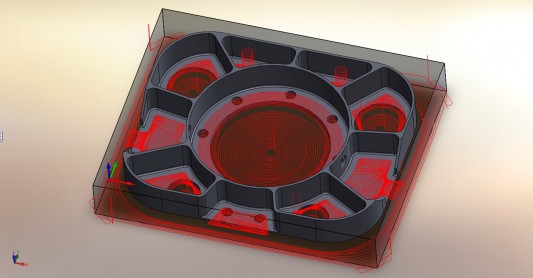
Most conventional CAM software will cut deep features in small steps to ensure the tool is not overloaded and to minimize the impact of over-engagement. With iMachining, CAM programmers can cut to the full depth of the tool in a single pass, as cutter engagement is optimized by smooth morphing tool paths, including morphing spirals. The software automatically avoids sudden direction changes and sharp corners, eliminating shock loading on the tool, and enabling the maximum volume of material to be removed in a single pass.
iMachining optimizes the feeds and speeds through for each individual component and setup, taking into account all the machine specifics (spindle power, max feed / speed), all the cutting tool data (number of teeth, helix angle, cutting length, tool material) and all the material properties. By combining all this information and then selecting the level of aggressiveness for machining—matching it to the rigidity of the setup—SolidCAM claims iMachining produces tool paths which will routinely halve machining times.
New algorithms within iMachining eliminate “air cutting”—the process of running at full speed but not cutting metal, and add the ability to subdivide pockets into areas that can be cut with iMachining’s morphing tool paths. The intelligent separation routines use new channelling tool paths to divide pockets up into areas that can be efficiently machined using the standard tool-paths which smoothly remove the remaining material.
More information is available in a PDF at the SolidCAM website.