Adding 3D part catalogs to PLM allows faster access to previously approved products.
[Editor’s Note: The following email interview with Part Solutions CEO Tim Thomas was finished right before leaving for the Planet PTC User conference. While there, I heard from more than one speaker about the need for greater emphasis on controlling design costs by more closely tracking part requisition. It turns out Part Solutions has been thinking about it as well.]
Part Solutions (they prefer PARTSolutions) is a provider of part catalogs based on 3D model data for manufacturers. The company’s key client is Boeing, which earlier this month won a place in the Progressive Manufacturing 100 list published by Design Automation for its implementation of a project called “Project Standards as Digital Data.” The project was a robust implementation of Part Solutions technology. Boeing estimates it saved itself $20 million in the first year of use, by reducing the time it takes engineers to find approved parts and by lowering the incidence of specifying new parts when existing ones will do.
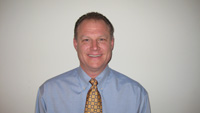
Part Solutions CEO Tim Thomas believes the Boeing deal is the tip of the iceberg for a new approach to product design that unites engineering and purchasing. In the following email-based interview, Thomas rehearses the history of CAD for product design as a way of explaining “purchineering.”
GraphicSpeak (GfxS): What has the evolution of CAD looked like from your viewpoint?
Tim Thomas (TT):We’ve come a long way since the days of the drafting board, when engineers and designers spent the bulk of their time with pencils in-hand. With its clear structure, this method was the only proven method for a number of years. It was also however, very time-consuming, requiring a great deal of preparatory work, as well as in-depth knowledge of best practices.
2D computer aided design rocked the engineering world. Engineers and designers could—for the first time—quickly create geometry without being totally dependent on “tribal knowledge.” Of course, the technology required a major investment, with every user requiring a CAD system.
Next, 3D computer aided design reshaped the landscape again. With its “easier than 2D” mantra, the 3D master model concept enabled engineers and designers to see geometrical ”volumes,” while offering more flexibility with several design methodologies. Design time was minimized with more intuitive operation, and the workflow was less rigid by eliminating the need for a standalone 2D CAD system. However, this approach leads to huge investments in CAD-specific training, and limits a company’s leverage when considering changes to those CAD dependent flailing processes.
GfxS: Where are we now and what’s led us here?
TT: Recently there has been a major shift in the way engineers are designing products. The need for lower product costs and faster time to market have placed great demand on product designers to work faster and smarter to produce designs that are more easily, quickly and cost-effectively manufactured.
Consequently, most manufacturers have adopted a PLM strategy centered on an integrated product model that incorporates manufacturing data. When combined with a 3D part catalog management solution, product designers and engineers are given direct access to catalog and custom parts directly from within their design (CAD) environment. This allows for design benefits like allocation of classes via clustering, readout of geometric attributes, sketch help and geometric search according to previously found objects—all of which have a profound impact on design time.
In addition, 3D part catalog management complements PLM by enabling parts or commodity reuse. Allowing configuration of 3D parts in native CAD formats within a larger PLM context gives designers the confidence to find, reuse and control standard parts more effectively. The reuse provided by CAD-native 3D part catalogs can be expected to reduce both IT management costs and overall product costs, including design, manufacturing and support costs.
But in many cases—even with a 3D part catalog in place—engineering still doesn’t know which parts are preferred. This leads designers to specify duplicate components in their designs that are not approved by procurement, or that are introduced in a way such that they become new components (in other words, new part numbers) that have to be sourced. The net result is an increase in direct material spending, adding not only to the cost of product development, but ultimately to the overall cost of goods sold (COGS) for the business.
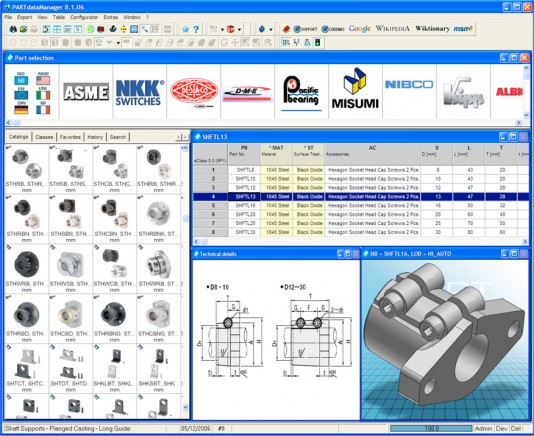
GfxS: What’s the next big thing?
TT: The next evolution in design is “Purchineering,” a symbiosis of standardized purchase processes and the application of preferred components by the engineering team. This newest concept in engineering is the first to impact not just designers and engineers, but the entire company.
From a design perspective, a formal policy of parts standardization and emphasis on use of parts from an approved parts list (APL) for certain commodities, allows for stability in the ongoing cataloging of parts, and gives designers the ability to find approved standard parts fast and with confidence. Not only does this reduce product development time, it also provides direction to the designer and eliminates a constant need to “reinvent the wheel” or redesign. It also affords suppliers and partners with the ability to easily cross-reference this information.
GfxS: What are the key benefits?
TT: By offering the ability to put more controls in place between Purchasing (buyers) and Engineering (specifiers), silos within a company are integrated, enabling companies to negotiate volume prices with strategic suppliers from which a company buys. This can have a particularly significant impact when considering that a 400 percent delta between high and low price for the same part is typical.
Additionally, it eliminates the introduction of parts that cannot be sourced in a timely manner, or prices for “one-off” purchases, and enables Procurement to maintain a list of items that can be standardized around the world in order to avoid as much downtime as possible. What’s more, engineers don’t need to become experts on part number schemas. Rather, they can find their parts based on geometric and performance data.
For these reasons, the use of standard catalog parts and the reuse of components across designs are having a profound impact on time to market and on total product costs. In fact, next-generation solutions that optimize how “standard parts” are managed and procured are allowing manufacturers to reduce their direct material spend by an average of 2% in the first year, while leveraging the ongoing benefits of a leaner inventory and the introduction of a formal parts standardization program that makes the designer’s job easier and more effective as well. It’s no wonder companies like Phillips, Bosch, Airbus and Boeing have all adopted the technology in order to make standard and buy standard.