No product specification sheets; no PR announcement until two months after it shipped; a list of new features that covers 34 pages; Universal Deformation Technology. What CAD product could possibly be defined by these characteristics? Finally, we let Rhino 4.0 out of its cage as our special series The Way of Rhino comes to a close. Originally published October 4, 2007 in CADCAMNET.
Editor’s Note, 2011: The other articles in this series are also available on GraphicSpeak:
Part 1: CAD Master Bob’s Most Excellent Launch Trajectory
Part 2: Behold the CAD Whisperer
Part 3: Tracking the coming perfect storm in CAD
By Randall S. Newton
CADCAMNET, October 4, 2007—Over the years I have met quite a few users of Rhino, the freeform 3D modeling software from Robert McNeel and Associates (RMA). Some are designers in Fortune 500 companies, others are self-employed artists. Some design buildings, some design shoes; many design consumer products. Rhino is also popular in movie studios and signature architecture firms. All Rhino users are passionate about their work, and can tell you in great detail why their 3D product is like no other.
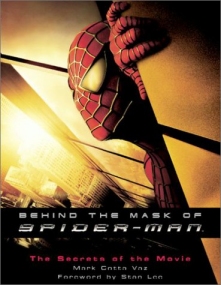
The one common characteristic of Rhino users is that they are designers of freeform shapes who want to define their ideas with extreme precision. With Rhino, says RMA’s Scott Davidson, they capture the “heart of their designs,” the unique styles, comfort elements, fashion, ergonomics, experience, etc. Some use Rhino to prepare shapes for analysis (CFD, FEA, mold flow, optical, etc.); others use it to de-feature designs created elsewhere before they are submitted to analysis. “The Swiss Army Knife market segment is ours,” says Davidson. “Everybody uses Rhino for something different.”
The Rhino ability to slice and heal slices on the fly makes it useful in rapid prototyping and related stereolithography applications. Several third-party products now support Rhino for CAM, and it is often found in shops using such reverse engineering and inspection tools as Microscribe, Roland, Romex/CimCore, and Faro.
Other specialty uses include:
- Illustration and animation—Spider-man for the movies was designed in Rhino; the product is often in joint use with 3DS MAX, SoftImage, LightWave, and Illustrator
- File Translation—RMA wrote their IGES translator from scratch
- Education—used in variety of disciplines where there are no standard CAD tools (as there are for engineering or architecture)
- Pure and applied scientific research—wherever modeling aids the research process.
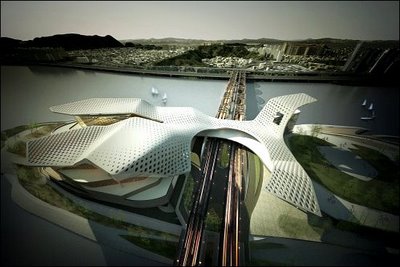
Passion for Version 4
Such passion existed before the release earlier this year of Rhino Version 4. When the shipping version was released, it was two months before RMA employees could take a break from order fulfillment and do typical things like publicly announce the new product. “I need to apologize for not telling everyone sooner that we were shipping Rhino 4.0,” explained RMA CEO Bob McNeel in a press release. “Our plan was to inform the beta users first, followed by the registered Rhino users, and then the subscribers to our newsletter and the public, all within a few days, but by the time we let the beta and registered users know we were shipping, we were overwhelmed.”
Most CAD companies make a big production of a product launch. Teams of marketing people, sometimes with the aid of an outside public relations firm, plan every detail. Some throw elaborate public events. RMA is different. Of the 40 employees in the Seattle headquarters, only two are marketing employees, and both spend time on other functions. RMA turns to a PR firm only occasionally. The majority are programmers and related development staff.
Soon after the release of Rhino Version 4 I saw Bob McNeel at COFES 2007 and we talked about this “oh, by the way” launch announcement. He said they had all hands in shipping for weeks, trying to get out the orders that rushed in when they announced Rhino 4.0 to the beta users. “We literally didn’t have time to do anything else,” McNeel said. “We were swamped.” Little wonder: Rhino Version 4 is easily the most significant new version in the product’s history. There are over 500 new features and enhancements. My cut-and-paste list of Rhino new features and enhancements is 34 pages long.
Rhino 1.0 was initially intended to be a high-end NURBS import tool for AutoCAD, and was thought of internally as “AccuModel.” One of the developers had a postcard with a photo of a rhinoceros on his wall, and RMA employees started referring to the product as Rhino. After using the name as part of a promotion at SIGGRAPH for a pre-release stand-alone version, the name Rhinoceros stuck.
Rhino Version 4 development strategy
Rhino Version 4 was more than three years in the making; most CAD firms today are on annual or 18-month development schedules. The other numbers that describe Rhino Version 4 are also out of the CAD industry norm:
- Number of new features or enhancement—500+
- Initial list of product specifications—0; no list was created
- Pre-beta testers—10,000.
“We don’t write product from specifications; users drive the development process,” says Davidson, who runs sales and marketing and is unofficially Bob McNeel’s right-hand man. If RMA had vice-presidents, (it doesn’t) Davidson would be “VP of loose ends, outreach, and whatever needs to get done.” For a commercial software company, the development of Rhino 4 seems to have been run more like an open source project. The users are field testers from day one, and anyone can communicate with the development team. Whenever possible, new features are plug-ins, not additions to the foundational product. There are no product managers. “Early customers set the priorities,” says Davidson. “We send out a lot of features and see where we should focus our 80% of labor to create the last 20% of a feature.” He says support and training personnel (many whom work for dealers, not for RMA) are “quite powerful” in setting product direction.
RMA no longer logs technical support calls; Davidson says the company solves issues faster as a result. If more calls start coming in about something, it is a signal to the staff to improve a feature so that the volume of calls will drop. “We can’t afford to not answer the phones,” says Davidson.
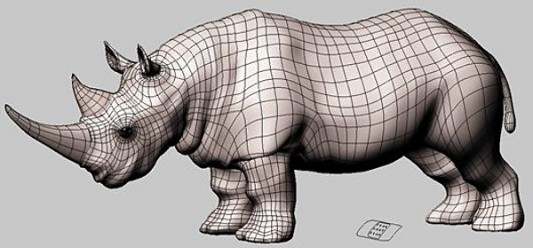
Davidson says RMA didn’t develop Rhino 4.0 from a specifications list, but the company did rely on foundational operational strategies to guide development. In a meeting with selected members of the press in May, Davidson and McNeel talked about the company’s strategies for product development, interoperability, technology, and industry standards.
Interoperability Strategy:
- Read/write as many 3D, 2D and raster formats as possible
- Provide anybody royalty-free libraries
- Provide SDK (software development kit) support for third-party developers
- Same SDK used internally as given to outside developers
Technology Strategy:
- Robust core based on NURBS
- Support point cloud and mesh data
- No license restraints on users or the company—license as little as possible to create the core product
- Make the development tools as open as possible—no intentional “black boxes” to third-party developers
Product Strategy:
- Uninhibited freeform 3D modeling—a modeling tool to describe what can’t be described in 2D
- Extreme accuracy at any scale (one user recently designed an electron microscope lens in Rhino)
- Compatibility with other CAD products
- As easy to learn to use as Microsoft Excel
- Fast operation on standard hardware (model size will vary performance on less powerful hardware)
- Robust development platform
- Affordability on many fronts—hardware, learning curve, lack of maintenance and support fees
All those new features
We won’t list the 34 pages of new features and enhancements here. Instead, the key to understanding Rhino 4.0 is a shorter list—ten technologies that allow all those new features to exist. There are short videos illustrating many of these on the Rhino website.
Universal Deformation Technology (UDT): A proprietary technology that allows the user to deform, without constraints, any curves, surfaces, meshes, and solids while maintaining the integrity of the object.
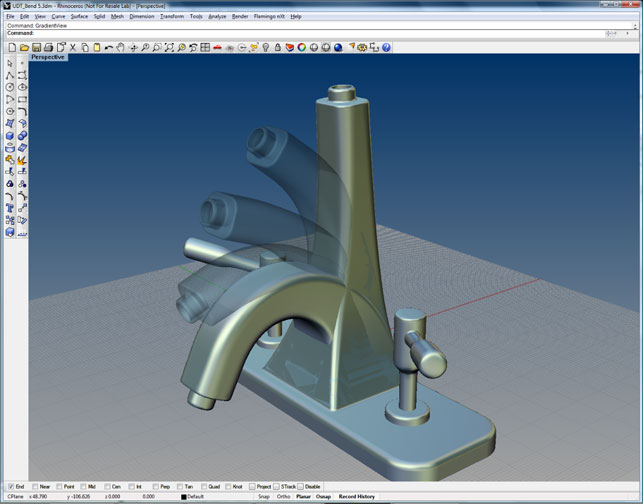
History: History-aware commands create geometry that can be edited by modifying inputs. History recording, updating of history-aware objects, objects with history locking, and warning messages can be toggled on or off. Not all geometry creation commands support history.
Feature recognition: It is now possible to automatically select all of the geometry of a specific feature when any part is selected (we’ve also seen this recently added to KeyCreator and NX). For example, a hole can be deleted or moved by clicking on any related geometry.
Display Pipeline: The new display pipeline takes advantage of the latest graphic card technology to provide a major speed improvement, new advanced display modes, real-time rendering, new analysis tools, multiple monitors, and support for new third-party application display modes. The new display pipeline also provides support for user-configured display schemes.
SmartTrack: A system of temporary reference lines and points drawn in the Rhino viewport using implicit relationships among various 3D points, other geometry in space, and the coordinate axes’ directions.
G-infinity: Provides designers with the tools to interactively adjust the shape of the blends while maintaining continuity beyond G2.
Filleting and Blending: Enhancements include continuity control between G0 and G4, new cross-section position and shape controls, fillet rail styles controls for Rolling ball, Distance from Edge, and Distance between Rails.
Intersection: Speed improved and more Boolean special cases are handled.
Toolbars and Docking: Toolbars and docking mechanisms have been completely rewritten, and conform to Microsoft standards. Docking toolbars, the command prompt, layer, properties, and other controls are easier to use and more reliable.
2D Drawing/Drafting Tools: 2D was a much-asked for feature by Rhino users. The new technology allows line styles, line weights, hidden lines, dimensions, hatching, page layout and printing/plotting.
Where Rhino goes from here
Later this month there will be a conference in London where designers from several world-class architecture firms will describe their use of Rhino on signature projects. The theme of the conference is “shape to fabrication”—the architectural equivalent of sending a manufacturing CAD model direct to milling or 3D printing.
So many of the ways Rhino is used could be considered “niche.” But in this day of widget-ware and Software as a Service, more and more users are looking to assemble a software toolbox, and they don’t expect one particular product to do everything for them. As the ranks of these users grow—and we believe they are growing rapidly—Rhino will be a major beneficiary.