Lockheed Martin and other leading aerospace manufacturers are banding together to promote a new view of interoperability. The goal is a data standard that unites design, manufacturing, and final assembly along one common digital thread.
First in a series
A new slant on interoperability is gaining ground in aerospace and defense (A&D) manufacturing, a concept called the digital thread. The phrase was originally coined at Lockheed Martin as a way to describe using 3D CAD data to directly feed computer numerically controlled (CNC) machining of parts, or a composite programming system (CPS) to create a plan for carbon fiber placement. In both cases the finished product can be traced back to the original computer model; the unbroken data link is the digital thread.
In an early interview on the subject Lockheed’s Don Kindard, development lead for the F-35, described the value of the original digital thread:
So, using the digital thread, I eliminate 6,000 tools, or 2,000 per variant, plus all the time it takes to do configuration management on those tools, plus finding them and getting them to the mechanic. Once again, because of the digital thread, I also eliminate mistakes positioning and locating brackets, which is normally one of our high drivers for quality.
A new industry consortium has formed to expand the idea of the digital thread beyond model-driven assembly. The Computation Manufacturing Alliance met for the first time at the AeroDef Manufacturing Conference earlier this month in Anaheim, California. The objective of the Alliance is to find companies whose technologies form significant links within a digital thread manufacturing philosophy, including 3D CAD, PLM, enterprise resource management (ERP), supply chain management (SCM), manufacturing execution systems (MES) and other technologies. The idea is to establish a common data exchange format structure with common interfaces from design to assembly. The goal is plug-and-play connectivity where data producers and data consumers will link to a common data source at any point in the manufacturing process. The Alliance looks to the day when any software product that is “Compufacturing Certified” is an assurance of working directly with data from any other certified product. The data standard will start at the design phase, extend through manufacturing, and continue through to final assembly.
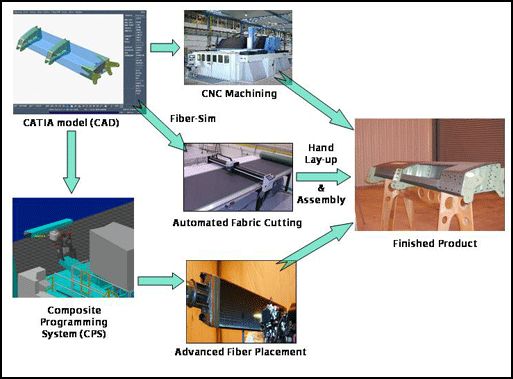
Potential for transformation
Mike Packer with Lockheed Martin Aerospace is one of the proponents of the new digital thread. As vice president of production operations for the Aeronautics unit Packer is responsible for production technology in nine facilities scattered across the US, employing 28,000 people. He is a member of the Executive Committee for AeroDef Manufacturing Exposition and Conference. The following is excerpted from a longer interview with Packer supplied to GraphicSpeak by the Conference, edited for clarity.
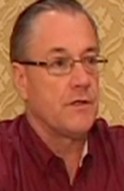
Question: How do you see the relatively new concept of the “digital thread” transforming aerospace manufacturing?
Packer: The teamwork required to create a digital thread does a number of things for our industry. For one thing, it means several partners have agreed to working from one common database, and everyone is working for the same goal.
If you think of it from a datum standpoint, that same digital datum that design uses as a reference point, we are using from a manufacturing process standpoint. If we construct everything around the same digital thread throughout the entire program, carrying everything into realization with actual product hardware, through field maintenance and field upgrades, we can make changes and bring modernization to the product itself more easily, because we are still using those same digital references.
The result of a digital thread is that we realize efficiency by avoiding the redundancy of recreating data as we did in the past.
The other real benefit of the digital thread is that now we can avoid the use of so much hard tooling and therefore reduce overall costs. You can’t totally eliminate hard tooling. Certain particularly sensitive or critical subassemblies have to come together in exact true positioning at tolerances that require a gauged assembly to verify if things are indeed aligned. But a manufacturer can eliminate a lot of the external tooling to position things, because you already know that the digital datum is employed within the numerical control system and the positioning equipment we use.
Whether it’s laser alignment, or numerically controlled machining and drilling processes, it goes right back to that digital thread, as opposed to manual drilling templates. We have eliminated all of that cost, all the maintenance, the keeping and storing and moving of those tools over the life of the program.
Question: What is the impact of the digital thread on the supply chain?
Packer: The concept of a digital thread is a huge help with the supply chain because it speeds up the transfer of data. Now they can pull up the model that comes out of our design database and start their manufacturing process.
When we have modernization or upgrade changes that come through, this information is immediately available to them in a physics-based exact solid model. With the thread, suppliers know there won’t be any interpretation in terms of the surfaces, they can trust that data as they employ it in their manufacturing processes. We don’t have all this transfer time, sending out new drawings and having the drawing checkers go through each change. They just pull it up on the screen and look at the new representation. The engineering notes identify that something has been modified, that something has been changed, or that another area remains the same. So they know how as a supplier, they can tie it into the adjacent assembly which they would also be assembling.