Automated generation of high quality meshes will aid CFD simulation for aerospace and other demanding engineering tasks.
The UK government, working with private software companies, recently finished a three-year study of advanced geometry handling and integration for industrial use. The study, known as GHandI (Geometry Handling and Integration), resulted in new capabilities in the automatic generation and use of a high quality mesh for computational fluid dynamics (CFD) simulation of the airflow around an aircraft.
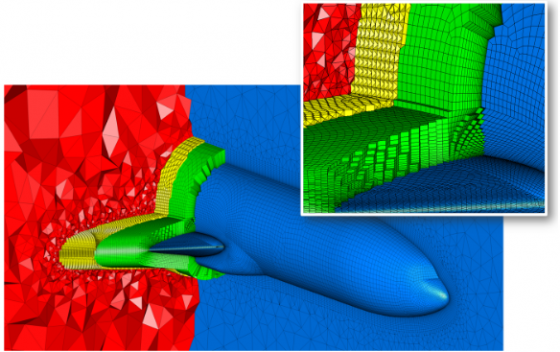
Significant contributions to the study were made using CADfix from ITI. According to Mark Gammon, technical director and CADfix product manager, CADfix made three key contributions: advances in the unique CADfix medial object technology, automatic domain sub-division of the air close to the aircraft skin into connected partitions, and the development of a framework for integrating best-in-class meshing technologies and external components to orchestrate the creation of a high quality hybrid CFD mesh.
“The results demonstrate the potential for real application in future aerospace programs, and extend to improving geometry handling for internal airflow simulation in aero engines, hypersonic simulation of missiles, and other advanced aircraft simulations,” says Gammon.
One of the most fundamental properties affecting the aerodynamic performance of a body is its shape. Demands for improved performance and optimization of airframe shape simulation and analysis continue to increase. ITI’s CADfix team worked with GHandI program partners, including Airbus and MBDA, to develop new capabilities for extracting information from geometry and adapting for use elsewhere in the aerodynamic simulation process.
“Improving aerodynamic modeling techniques is becoming increasingly important,” says Robin Addison, a GHandI project leader from MBDA UK. “The results from the GHandI project and the advanced geometry handling and meshing technology developed give us the critical building blocks needed to innovate the next generation of aircraft.”
“The success of this initiative is meaningful for both the aerospace industry at large and for ITI,” adds Gammon.
A full technical analysis of the GHandI study is available from ITI: http://hubs.ly/H03-4_S0